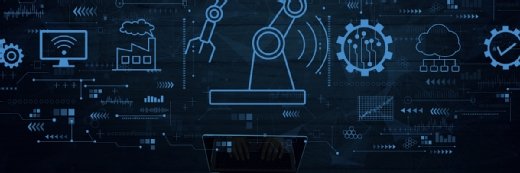
Getty Images/iStockphoto
5 ways IoT can improve manufacturing downtime
Downtime is expensive and disruptive to manufacturing companies. IoT can help managers use real-time data and reports to catch issues before they happen.
IoT technology in the manufacturing industry lets businesses implement digital transformation. The technology includes advanced sensor devices, gateway connectivity, and a dashboard for the managers to simplify their workload and improve all aspects of industrial production.
It can be quite difficult for manufacturing industries to keep an eye on machine health. It affects performance, and when a piece of equipment causes failure or faces downtime, it disrupts production, incurs costs and damages business processes.
It is usually caused by unplanned maintenance of the machine, tool breaks, undefined adjustments and unattended leakages. Every minute the machine is left unaddressed during its downtime phase, excess revenue is likely to get lost.
Such challenges discourage production and cause untimely delays, leading to huge maintenance costs. The managers thus seek a better solution upon which they can rely and gain valuable insights to minimize the challenges – and IoT technology is one option.
IoT in the manufacturing industry
The manufacturing sector is loaded with giant pieces of machinery and all kinds of equipment that contribute to the production process. IoT technology uses sensor devices, gateway connectivity and an operable dashboard, which form a complete IoT architecture that gets installed with the existing industrial setup. This setup provides a reliable source of processing with the industrial operations according to managerial, manufacturing or business parameters.
A main goal of IoT within manufacturing is smart factory creation. Many manufacturers opt to install smart software within their businesses and IoT technology. It strongly boosts a brand image for any business and ensures productivity along with scalability. IoT transforms many industries through advanced techniques; manufacturing is no exception.
How IoT technology improves machine downtime
With IoT technology, industrial tasks can become easier to handle, and it lets managers have enough bandwidth to make appropriate decisions. There are five main ways IoT can improve machine downtime.
1. Data-driven approach
The use of a data-driven approach to track industrial assets provides measurable advantages. Currently, IoT technology collects data to gain informed insights about manufacturing equipment and processes. This data increases the chances of accurate decision-making, which enables the managers to improve their business at significantly low costs.
Installed sensors support a data-driven approach to provide the businesses with correct insights based on relevant information. Managers use such information to extract certain patterns and become fully aware of their business and plant goings-on. With these patterns, managers have a sort of security toward assets and can handle everyday challenges seamlessly.
2. Predictive maintenance
Predictive maintenance with IoT technology minimizes the number of machine breakdowns, maximizes asset uptime and improves asset reliability. It can also reduce operation costs, as it requires maintenance only when necessary. IoT-based predictive maintenance optimizes the timing of the equipment condition, which ensures large cost savings. The IoT-based offerings use specifically designed algorithms to improve production floor configurations.
Moreover, the industries that use smart offerings to predict timely machine downtimes also benefit from anomaly detection. It enables floor managers to keep a strict eye on the machine conditions -- even at remote locations.
3. Real-time and remote monitoring
IoT provides real-time monitoring to industrial assets and smart task management. It helps optimize and improvise the processes that manufacturers carry out through accurate data extraction and converts data into a user-readable format for managers to effectively make decisions.
It also streamlines the abilities of the entire plant to a single dashboard, which enables the managers to simplify their work at a low-cost budget. It further helps detect the excess vibrations in the machines, which might cause unplanned downtime.
The sensors get installed over the appropriate assets to gain data and information, such as equipment health, temperature, pressure and operating conditions, in real time. This lets floor managers be quick in their actions whenever they find a fault within the machine or schedule timely equipment maintenance to limit downtime.
4. Advanced analytics
IoT is advancing industries through data analytics, enabling convenience to the managers in their workload. Research from McKinsey noted that advanced analytics helps predict machine breakdown before the event might occur and can reduce the overall downtime between 30% and 50%. It further increases the equipment life by approximately 40%, thus improving industrial productivity in all aspects.
An IoT-powered manufacturing software comes in handy with advanced analytics, which uses sophisticated techniques and tools to discover informed insights, make accurate predictions and generate recommendations through reports. Advanced analytics through IoT technology unleashes productivity and profitability within the industry to reduce machine downtime occurrence.
5. Illustrative report generation
IoT-powered manufacturing installations help managers to make effective decisions through various illustrative reports that gather and state all the required data. The smart industrial offering for the manufacturing sector involves sensors to extract asset data, gateway connectivity to transfer that data and a dashboard to enable operations. During the whole process, there are report generation options that mention all the details for the managers and encourage effective decision-making.
The reports illustrate an understanding of the overall manufacturing floor, such as machine conditions, temperature requirements, humidity control, vibrations, noise and excess resource waste. These reports -- and IoT -- thus provide effective control over everything related to the plant operations and positively affect business productivity and profitability.
About the author
Sanjeev Verma is founder of Biz4Intellia, one of the leading IoT development companies in the U.S. He is extremely passionate about IoT and keeps exploring the possibilities unleashed by IoT on a constant basis. At Biz4Intellia, his concrete focus on building a rapidly growing, market-driven organization that delivers influential enterprise IoT solutions is simply unmatchable.