What is a smart factory?
A smart factory is a highly digitized and connected production facility that relies on smart manufacturing. Thought to be the so-called factory of the future and still in its infancy, the concept of the smart factory is considered an important outcome of the fourth industrial revolution, or Industry 4.0.
Used by manufacturing companies, a smart factory works by employing technology such as artificial intelligence (AI), robotics, analytics, big data and the internet of things (IoT). It can run largely autonomously with the ability to self-correct at the edge.
Characteristics of a smart factory
The defining characteristics of a smart factory are visibility, connectivity and autonomy. Factories have long relied on automation, but smart factories take this concept much further and can run without much human intervention.
Through the use of modern technologies, smart factory systems can learn and adapt in near real time or real time, enabling factories to be far more flexible than those of the past.
Smart factory technology and processes
Extensive use of IoT sensors and devices connects machines and enables visibility into their condition as well as into factory processes, creating an industrial internet of things (IIoT). Increasingly sophisticated analytics and applications based on AI and machine learning handle many of the routine tasks, freeing up people to focus on handling exceptions and making higher-level decisions. Robots are expected to populate smart factories for routine work, working alongside people.
Smart factories rely on smart manufacturing, which connects the plant to other entities in the digital supply network, enabling more effective supply chain management. They also rely on digital manufacturing, which uses a digital twin to connect a product digitally at all stages in its lifecycle.
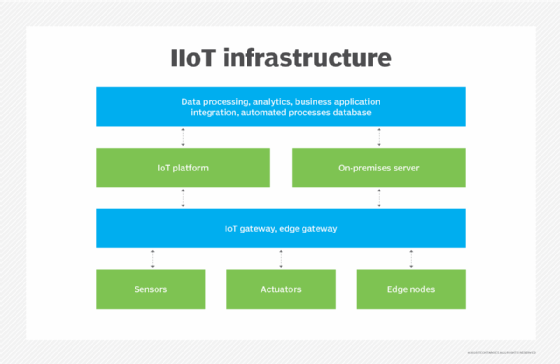
In addition, production machines can be used in the local network of a manufacturing execution system to receive orders, report progress, access work instructions, and interact with quality and traceability systems. Plant floor workers can more readily see important information such as instructions, schedules, quality data, inventory status and demand changes.
In the vision of a fully connected smart factory, each facility is linked to the others, and the entire enterprise is linked across departments as well as externally to customers and suppliers. In this way, companies can monitor needs and activities, and collaboration is enabled across the extended enterprise to increase speed and efficiency.
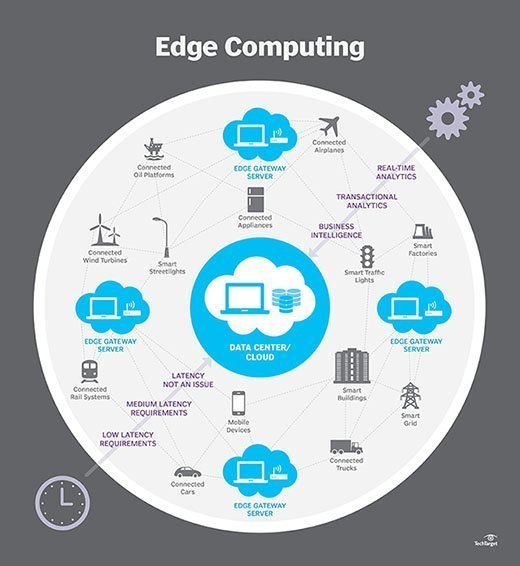
Smart factory benefits and challenges
A fundamental characteristic of a smart factory is its connectedness, where sensors link devices, machines and systems to provide real-time data for decision-making.
In a similar way that smart home devices accomplish routine actions like dimming lights at a certain time or triggering alerts when something is amiss, the ideal smart factory runs itself on a much larger scale, self-correcting where appropriate and alerting for human intervention when needed.
In addition, the extensive data generated offers real-time insights to supply chain stakeholders, enhancing agility and enabling proactive issue resolution. IoT technologies have already proven beneficial in monitoring industrial operations, providing supply chain visibility and predicting equipment downtime.
Technologies to create a version of the smart factory already exist, and early adopters are exploring the benefits. However, widespread adoption faces several challenges, with data integration being a significant issue. Creating a connected manufacturing and digital supply network requires managing massive amounts of data from various components across different industries and formats.
Let's delve a bit more into the benefits and challenges of smart factories.
Benefits
Enhanced efficiency. Smart factories significantly enhance operational efficiency by employing automation, AI, real-time monitoring and data analytics. This enables streamlined processes, reduced downtime and optimized resource allocation.
Increased flexibility. Smart factory systems can learn and adapt in real time, enabling them to handle various production tasks with minimal human intervention. This flexibility is crucial for meeting the demands of a dynamic market environment.
Improved quality control. By using advanced sensors and machine learning algorithms, smart factories can monitor production quality in real time, identifying and addressing defects or anomalies immediately. This leads to higher product quality and reduced waste.
Better supply chain management. Integration with the digital supply network enables smart factories to better manage inventory, forecast demand, and coordinate with suppliers and customers, resulting in a more responsive and resilient supply chain.
Challenges
High implementation costs. The costs of implementing smart factory technologies can be prohibitive, particularly for small and medium-sized businesses. These costs include not only the initial investment in hardware and software, but also the ongoing expenses related to maintenance, upgrades and training of personnel to effectively use new systems.
Data integration issues. Creating the ideal connected manufacturing and digital supply network embodied by the smart factory requires dealing with massive amounts of data from different components in diverse industries and formats.
Cybersecurity risks. Increased connectivity also raises the risk of cyberattacks, which can compromise sensitive data and disrupt operations. Ensuring strong cybersecurity measures are in place is crucial for protecting the integrity of smart factory systems.
Resistance to change. Achieving buy-in from business leaders and employees can be challenging. There might be skepticism about the return on investment and concerns about potential disruptions to existing processes. Demonstrating the tangible benefits of smart factory initiatives is essential for overcoming this resistance.
With the rapid pace of technology developments building in this area, including in human-machine interfaces and better analytics, more businesses are expected to look for ways to create smart factory endeavors.
AI and IoT are key parts of the Industry 4.0 -- and therefore the smart factory -- ecosystem, and the possibilities that exist for the two functioning together are endless. Explore different ways in which AI and IoT technologies work together and how AI supercharges existing IoT systems. Also, learn more about potential IIoT use cases as well as more of its advantages and challenges.