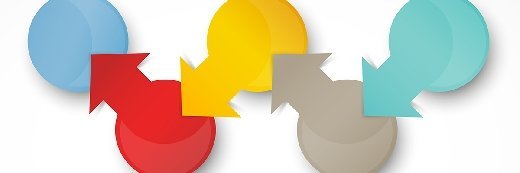
Fotolia
What supply chain issues most worry discrete manufacturers?
Discrete manufacturers face challenges related to demand forecasting and inventory management, to name just two. Here's a look at why -- and what can be done.
Discrete manufacturing companies -- from makers of electronics, automotive, industrial equipment to 747s -- all have their particular challenges.
Still, as discrete manufacturers, as opposed to process manufacturers, they have many supply chain issues in common. Here are four:
- Demand forecasting. The demand for configure-to-order and build-to-order products is inherently variable. Original equipment manufacturers (OEMs) tend to forecast at an aggregate family level and poorly forecast component attach rates. This puts component suppliers at a disadvantage, since they are at a distance from end-markets and therefore often have no visibility into the factors that influence customer demand. This lack of visibility affects their service levels, with specific part or raw material shortages popping up unexpectedly. Moreover, a variable supply affects the cost to serve.
Some approaches that can help deal with supply chain issues are marketing intelligence about the end markets and collaborative forecasting beyond the OEM to dealers' and retailers' data. - Inventory management. Similarly, and often due to demand data issues, inventory is hard to manage in a discrete manufacturing supply chain. Although the brand manufacturers boast build-to-order, the reality is these chains are build-to-stock, with suppliers carrying the burden of inventory.
There are a variety of causes and remedies to managing inventory and various supply chain issues, but lean practices with an emphasis on cycle time reduction as well as demand planning are key solutions.
- New product introduction, time to market. Whether building the new Dreamliner 787 or a cool new smartphone, the ability to meet time-to-market goals is a huge challenge. Varying production approaches up and down the supply chain along with poor data sharing affect key metrics such as time to market for new product introductions. Companies find it challenging, as well, to forecast new products.
Product lifecycle management planning and forecasting systems have been shown to produce positive outcomes in planning launches and initial inventory requirements. - Service management. Due to the distributed nature of customers, who have purchased a huge variety of unique products and components, service management is a huge issue. The ability to plan service parts and build and manage a responsive service network remains a preoccupation for the manufacturer, and an ongoing expense to the customers.
Service Lifecycle Management with key modules such as multi-echelon inventory management service logistics, and service technician mobile systems can help.