FMEA (Failure Mode and Effects Analysis)
What is FMEA (Failure Mode and Effects Analysis)?
FMEA (failure mode and effects analysis) is a step-by-step approach for collecting knowledge about possible points of failure in a design, manufacturing process, product or service.
Failure mode (FM) refers to the way in which something might break down. It includes potential errors that might occur, especially errors that could affect the customer. Effective analysis (EA) involves deciphering the consequences of those breakdowns. It does this by ensuring all failures can be detected, by determining how frequently a failure might occur and by identifying which potential failures should be prioritized. Business analysts typically use FMEA templates to assist them in the completion of analyses.
Used as a risk assessment tool, FMEA has a scoring scale of 1-10. A one is a sign of low risk, while a 10 is a sign of a very high risk.
For development and manufacturing organizations, FMEA is an effective method of lowering the possible failures in phases of the product lifecycle.
Types of FMEA analyses
There are three main types of failure mode and effects analysis.
- Design FMEA (DFMEA). This focuses on how to prevent or mitigate possible system, product or process failures. DFMEA is used to determine potential failures, how bad the effect could be, and how to prevent and mitigate failures. This process helps engineers detect failures early on so they can be corrected without being costly.
- Process FMEA (PFMEA). This focuses on identifying potential risks to process PFMEA helps identify process functions, failure modes and effects to help organizations understand possible risks for each process step as early as possible.
- Functional FMEA (FFMEA). This focuses on avoiding possible failures before corrective actions must be taken. FFMEA identifies and prioritizes potential functional failure modes.
When to use FMEA
A business analyst might perform an FMEA when a product or service is being designed or fixed, or when an existing product or service is being used in a new way. FMEA can also be used before developing control plans for a new process or following a quality function deployment. Lean production methodology uses FMEA periodically throughout the lifecycle of a product or service. FMEA can also be used to identify and mitigate potential hardware risks as well.
FMEA is generally used in situations where improvement goals are implemented, or when designs, changes, new features, regulations or feedback is given -- as this is where potential failure and detection can occur.
Benefits of using FMEA
FMEA offers organizations the following benefits:
- gives them an early way to identify and mitigate potential modes of failure;
- minimizes the need to make late changes to a project due to potential issues;
- reduces the risk of a problem happening more than once;
- provides prompts for employees to follow when facing a potential failure mode;
- promotes more collaboration among teams that handle areas such as design, manufacturing, quality, testing and sales; and
- reduces the cost involved by avoiding fixing issues in development.
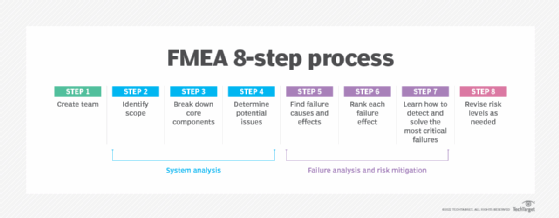
FMEA procedure
Failure mode and effects analysis might be implemented differently, depending on the organization. As such, the number of steps involved may also differ by organization. As a general process, FMEA steps include the following:
- Create a team of employees who have collective knowledge or experience with the system, design or process and customer needs. This includes employees with experience in customer service, design, maintenance, manufacturing, quality, reliability, testing and sales.
- Identify the scope of the system, design, process, product or service. Define the purpose of the system process, service and design.
- Break down a system, design or process into its different components.
- Go through system, design or process elements to determine each possible issue or single point of failure.
- Analyze the potential causes of those failures as well as the effects the failures would have.
- Rank each potential failure effect based on decided criteria such as severity, likelihood of occurrence and probability of being detected. Organizations can use a risk priority number to score a system, design or process for risk potential.
- Determine how to detect, minimize, mitigate and solve the most critical failures. This helps keep failure effect risks low by creating a list of potential failures and corrective actions to take.
- Revise risk levels as needed.
Learn more about event-driven failures, including some different types of failures and some potential ways to handle event-driven architecture failures.