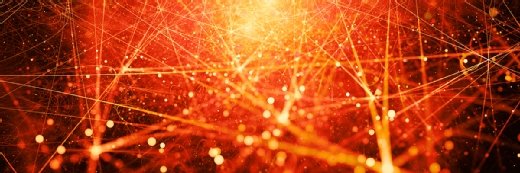
Getty Images/iStockphoto
New ways of upcycling CO2, decarbonizing steel and cement
The industrial sector has a massive carbon footprint. That's why some companies are working to clean up steel and cement and find new uses for carbon.
Finding greener alternatives is critical to lowering global greenhouse gas emissions. That's especially true in the industrial sector.
Carbon dioxide, or CO2, is one of the main drivers of the climate crisis, and the industrial sector is a main offender. For example, heavy industry -- including steel and cement -- produces almost 40% of global carbon dioxide emissions, according to the Brookings Institution. That's why one track of the MIT Technology Review's inaugural ClimateTech conference, held Oct. 12-13 in Cambridge, Mass., focused on decarbonizing cement, decarbonizing steel and turning carbon into jet fuel and other products.
Here's a look at these innovations.
1. Decarbonizing cement: Sublime Systems
Cement is ubiquitous, and its creation and use has a negative impact on the planet.
Cement produces 8% of global carbon dioxide emissions, said Leah Ellis, CEO of Sublime Systems, located in Somerville, Mass., during a session at ClimateTech.
"It's also one of the most difficult things to decarbonize," Ellis said.
Creating one kilogram of cement produces the same amount of carbon dioxide, said Sublime Systems' Yet-Ming Chiang in an interview with MIT. Standard cement is created by burning coal to heat up limestone, sand and clay. The burning coal and the gas from the hot limestone both create carbon dioxide.
Sublime Systems uses a different approach. The company uses ambient temperature electrochemistry to create cement. This process reduces the amount of carbon produced in comparison with the usual way of producing cement.
Sublime Systems aims to make a form-fit-function replacement for Portland cement, which is the most frequently used type of cement, Ellis said.
If something is a form-fit-function replacement for another item, it has the same form, or traits like size and measurements; the same fit, or the ability to attach to another item; and the same function, or the ability of the item to carry out a task.
Scaling is currently a major focus for the company.
The organization has gone from lab scale to pilot scale over the last two-and-a-half years, Ellis said, and the company at pilot scale will produce between 10 to 100 tons of their cement per year. However, the company must produce a million tons per year to be competitive with the rest of the industry.
"Scale is everything," Ellis said. "We have a goal of having a swift and massive impact on climate change by getting to scale as quickly as possible."
Sublime Systems is not the only company working to decarbonize cement. A number of organizations are working on green cement offerings. Now the question is whether construction companies will embrace the new options. Cost and the question of whether cement substitutes will meet with approval from regulatory bodies, which is still unknown, could factor into potential adoption.
Another strategy for improving cement's carbon footprint is for companies to produce cement the traditional way, then store the resulting carbon using carbon capture technology.
However, using Sublime Systems' approach is less expensive than following that strategy, Ellis said.
"We think we can compete with today's cement at scale in the future," Ellis said. "We know for sure that we're going to be less expensive than cement plus post-combustion carbon capture, which will double the price of cement."
In addition, carbon capture is likely more problematic and complex than using methods that produce less carbon in the first place.
2. Turning greenhouse gas into products: Twelve
Carbon dioxide is now best known to the world as a cause of global warming which is generated through production, among other sources. Twelve, located in Berkeley, Calif., uses carbon transformation technology to turn carbon dioxide into substances like fuel, with oxygen and water as the technology's sole outputs. Twelve can work with partners to help them create products that would otherwise require oil. For example, the company paired with Mercedes-Benz to create car parts.
Twelve is currently scaling up, said Kendra Kuhl, CTO of Twelve, during a ClimateTech session. The organization has recently announced partnerships with Microsoft and Alaska Airlines to scale up E-Jet, Twelve's jet fuel technology, and with Virgin Voyages to scale up E-Marine, Twelve's fuel product for cruise ships.
"At full scale, [our carbon transformation] technology would mitigate about 10% of the world's CO2 emissions," she said. "[With Twelve] making enough fuel to fly a commercial flight or a cruise line, that's still an extremely small amount of fuel compared to the amount of fuel that's used."
As Twelve scales up, the more easily accessible sources of carbon dioxide may disappear, but Kuhl doesn't see that as a major problem.
"As you're making more and more product, then I think that that lower-hanging fruit -- more concentrated and pure sources of CO2 -- do get used up," she said. "But I think there will still be plenty of CO2 around for us for a while."
3. Decarbonizing steel: H2 Green Steel
H2 Green Steel, which is located in Stockholm, is tackling another industry that has historically produced a lot of carbon dioxide. The company plans to take multiple newer approaches, including using green hydrogen instead of coal and using electric arc furnaces, to make their steel. H2 Green Steel's goal is to begin large-scale production by 2025.
Demand for this green steel reaches across multiple industries, said Maria Persson Gulda, CTO of H2 Green Steel, during a ClimateTech session. Gulda believes this demand comes from leaders learning about the recent EU ban on cars with combustion engines, which will take effect in 2035.
"They are afraid that the same will happen to steel," she said.
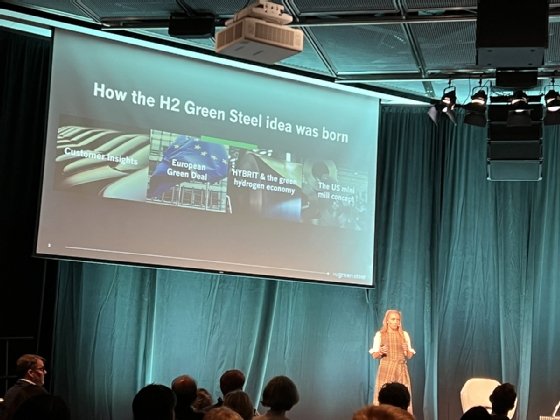
The European steel industry has not switched to using green electrons before now because the lack of needed resources in most areas would make it a costly change, Gulda said. Green electrons are not continually available in many countries.
"Only the north of Sweden and the north of Norway is suitable for this transition today," she said.
While H2 Green Steel is not yet in production, the company is using data from partner organizations that carry out similar processes to attempt to prepare for its own production. In turn, H2 Green Steel helps the other companies improve their production.
"When we are up and running in 2025, we already will have a model that can be tweaked," Gulda said in a TechTarget interview.