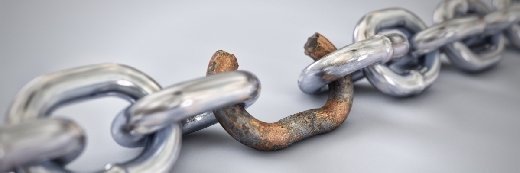
James Steidl - Fotolia
Supply chain applications help ease COVID-19 crisis
Supply chain applications from SAP Ariba, SourceDay and Kinaxis are helping companies find critical PPE, maintain manufacturing lines and plan for supply chain risk assessment.
Supply chains around the world have been disrupted by the COVID-19 crisis; however, supply chain applications are proving their worth in helping organizations weather the disruption.
In fact, supply chain applications that were valuable before the COVID-19 crisis hit have become critical players in securing needed supplies and keeping parts flowing for manufacturers.
ViaQuest, a home healthcare provider based in Dublin, Ohio, was desperately searching for personal protective equipment (PPE) and was able to secure several hundred protective goggles by using the SAP Ariba Spot Buy supply chain application.
ViaQuest found SAP Ariba Spot Buy through Premikati, an SAP Ariba partner that provides procurement consulting services for primarily small to midsize organizations that don't typically require their own in-house supply chain applications.
"Everybody in the medical field is trying to get their hands on PPE because you have to have new garb for every patient that you see," said Amanda Overmyer, vice president for sales at ViaQuest. "We tried to be preemptive and get ahead of the curve and put orders in, but everything was on back order. You're just in a queue and when it's your turn to get the delivery, you get the delivery."
Desperately seeking PPE
Overmyer acknowledged that she knows nothing about SAP Ariba or procurement, but she was acquainted with Chad Buchanan, Premikati's COO.
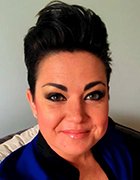
"I knew that he got things for people when they needed it, and in an act of desperation I called him up and explained my problem and asked if he could help," she said. "He said he needed an email and a credit card, and 10 minutes later I had an account. Fifteen minutes later, I'd put in an order and he was able to find the goggles that we needed."
Premikati used an SAP Ariba application called Spot Buy to locate and procure the goggles. Spot Buy is a B2B marketplace that lets users search through millions of items from vendors vetted by SAP Ariba, along with negotiated prices.
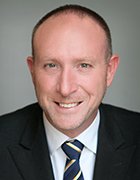
"They go through a search bar just like any other online shopping, type in whatever you'd like," Buchanan said. "Spot Buy will bring up item pictures and the vendors -- a number of them, so you can pick through and see the shipping policy, return policies, things like that."
Although using Spot Buy was a possible life-saving experience for ViaQuest, it can also be valuable for the new normal working situation that companies and employees find themselves in now.
"You can use this for anything, not just PPE products," Buchanan said. "The reality is that organizations are now having their employees work from home. With Spot Buy, you can put a shipping address in per individual; so, if you have 200 people working from home and you need to get them a laptop or whatever, this is a very easy and quick way to accomplish that."
Prioritizing critical parts
Supply chain applications are also helping alleviate some of the disruption to manufacturers caused by the COVID-19 disruption.
Global Interconnect was able to keep manufacturing operations running by using SourceDay, a supply chain management application that allows buyers and suppliers to collaborate and exchange real-time data on things like prices, inventory stocks, order lead times and delivery dates.
Global Interconnect, a firm based in Pocasset, Mass., designs and manufactures custom cables and connectors for electromechanical devices for primarily the medical industry and high-end industrial OEMs. The company operates several manufacturing facilities in China and ships parts from suppliers in the U.S., and was disrupted early in the crisis when China was affected.
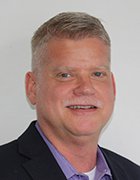
"When COVID first hit, we first got word of it in January when people in China were just getting ready to leave for Chinese New Year," said Troy Mauk, Global Interconnect's director of global procurement. "Our factories every year shut down for about two weeks anyway, but they completely shut down."
The company had extra stock to cover the shortages from the planned Chinese New Year shutdown, but returning the manufacturing facilities to production has been very slow, Mauk said.
"Even when the factories started to open over there, it wasn't just like everybody was running back to work; it depended on where you were," he said. "So, it was very slow starting up. Most of ours are back up and they're still bringing in people, but they have a 14-day quarantine before they could even go in the factory."
In one night, the status of every order was changed to "late delivery," which could have brought the entire operation to a standstill. Mauk turned to SourceDay, which enabled Global Interconnect to prioritize the most important parts.
"I looked at everything that was due by March 27 in SourceDay, and then used their Hot List and put everything that was a priority on the list," Mauk said. "The Hot List was the true source to my suppliers for what they need to concentrate on -- 'Don't worry about the lates, don't worry about what's coming up, you've got to worry about what's on this Hot List because that's what's going to keep our supply chain up and running.'"
Global Interconnect always makes safety stock, but this could be set aside temporarily to focus on only the most needed parts, Mauk said.
"I really looked at every part, and it was just for safety stock and not true demand. It didn't go on the Hot List," he said. "I had to get my true demand on the Hot List, and that's how we managed our suppliers during this whole thing."
Planning for different supply chain scenarios
As the crisis continues to unfold, companies will need to fully understand their supply chains and be able to plan for a variety of potential scenarios. Kinaxis offers comprehensive supply chain planning and management applications that enable companies to create digital twin models of their supply chains.
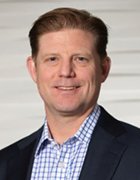
They can then use these supply chain digital twins to determine the best courses of action for various events, such as the COVID-19 disruption, said Jay Muelhoefer, chief marketing officer at Kinaxis.
The Kinaxis platform integrates with ERP systems such as SAP and coalesces all the various data from supply chain silos, such as demand planning or supply capacity. These typically operate independently from each other and use different data models. Each supply chain functional area subsequently creates its own version of the truth, and tend to be out of sync with each other, Muelhoefer said.
"The demand area creates one projection of the future; supply then takes that and creates a new projection, but the meantime the demand signal has changed, so you have competing versions of the truth and a limited ability to do analytics," he said. "This impedes making accurate decisions on what actions you should take for your supply chain based upon variation, and when you have an extreme disruption like right now with COVID-19, it becomes absolutely critical to be able to do replanning in minutes, not weeks."
The digital twins can model all of a company's plants, sites and distribution facilities, and you can have the models calculate responses for different scenarios, Muelhoefer said.
"Let's say all of a sudden now your manufacturing supply shipping from China stops," he said. "Do you want to meet customer requirements and satisfy orders for large key suppliers, or do you want to [spread out] that supply across a number of people and only do partial orders?"
Ultimately, the COVID-19 crisis will change the way that companies deal with supply chain risk, and they will need to prepare for the new normal, Muelhoefer said.
"The impact has been so dramatic that boards are going to be demanding that there's a supply chain risk management plan that's added to their governance, risk and compliance list," he said. "That's preparing for the new normal so that if something like this or other major disruption happens, how you can better respond and reduce the risk profile."