Artificial intelligence and the connected plant
The connected plant is a crucial component of the internet of energy, but what exactly does it entail? A connected plant means linking physical assets or machinery under management with operators responsible for their production, efficiency, security and safety — in sum, utilizing modern technologies to improve value and collaboration.
Right now, however, the connected plant is mixed in buzzword stew with little cohesive strategy. There is the cloud, the fog, wearables, drones, IoT, IIoT, 3D imaging, geofencing, wireless, apps, smart tags and other technology trends that may or may not be beneficial to a company’s specific needs. Plants may adopt new technologies based on mandates, but lack a cohesive strategy to accompany the digital transformation and see the true value of the tech.
So where does artificial intelligence fit into this litany of potential technologies? Honestly, in all of it.
Drones, artificial intelligence and wind production
One mature area widely using artificial intelligence is image recognition. Currently utilized for lane detection in cars, facial recognition and tagging on Facebook, and monitoring the health of crops via drone imagery, image recognition is also being used in identifying blade damage on a wind turbine.
Drones are poised to deliver significant impact for wind maintenance and safety. According to Navigant Research, the “cumulative global revenue for wind turbine UAV sales and inspection services is expected to reach nearly $6 billion by 2024.” This is a huge opportunity and the use of artificial intelligence is at the forefront.
Only 39% of executives say their organization understand the risks and opportunities of important digital trends.
— Bain Brief, ‘Digital Strategy for Utilities‘
Let’s explore an example of blade inspection via digital imaging and drones. High speed, high-resolution cameras mounted on drones capture several thousand images of the turbine. The captured images are input into a convolutional neural network, a type of deep learning approach, to train and automatically recognize failures without human intervention. Given enough images, not only is identification possible, but the system starts classifying the types of failures and predicting when required maintenance is necessary.
Drones utilize geofencing to fly to the same location and perform the same inspection routine over and over. An operator never needs to leave his truck or climb a tower, and consistent results void of human inconsistencies are analyzed by algorithms. The software raises alarms based on images from the drones, and skilled operators now apply their expertise to diagnose the nuances of the degradation.
Using drones reduces operation and maintenance costs in a number of ways. Drones boost worker safety because they can fly in potentially dangerous areas, reduce vehicle fuel costs and have a scant environmental impact.
Wearables: The new source of predictive data
The human body is by far the most critical asset found in a plant, yet there are still nearly 300,000 people who die from occupational accidents each year.
The use of wearables is merging human safety with artificial intelligence to provide predictive or preventive maintenance on humans. For example, in a recent pilot study by IBM and North Star BlueScope Steel, plant managers can observe heat stress and exertion in users by monitoring sources of data like body temperature, heart rate and activity levels.
Similarly, mining company Rio Tinto is piloting SmartCap, a device that looks similar to a baseball cap and conducts regular EEG tests on the wearer. It measures worker fatigue, for example, when truck drivers working long shifts are reaching sleep exhaustion levels.
In both examples the technologies produce data, only now the information isn’t coming from sensor data on a mechanical machine, but from the ultimate machine: the human body. With data comes the capability to perform analytics from simple threshold analysis to complex machine learning approaches. Algorithms start learning normal, or baseline, behavior as well as identifying anomalistic body operating conditions. These wearable systems can then alert management to critical issues or impending dangers.
“Nearly 300,000 people still die from occupational accidents each year.”
While safety is of utmost importance, wearables also boost employee efficiency. Technologies like smart hard hats and smart glasses provide real-time information capabilities to augment workers’ knowledge with a hands-free interface. SparkCognition, for example, has shown the worker of the future looking something like this:
- An operator scans the connected plant and is directed via visual cues to a failing asset (a pump in our demonstration).
- Once identified, the operator utilizes a pop-up, hands-free interface to visualize real-time operating conditions and historical trends.
- The operator can then display maintenance records and work orders previously performed on the pump and load detailed schematics about the asset, all viewed on the virtual interface.
- Finally, if the operator is still unable to make a clear determination on the issue they can “phone a friend” and get a direct line to the pump manufacturer’s support portal where experts help resolve the issue in real time.
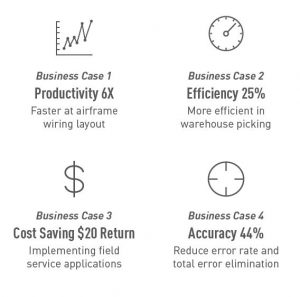
Figure 2: Smart glasses productivity potential for various connected plant initiatives. Source: Vuzix Corporation.
What used to take days to fix and diagnose can now be done in minutes. But this technology comes at a cost. When collecting human biometrics, it’s extremely important to ensure the privacy and security of the information being collected about personnel. Guidance for responsible utilization needs to be transparent at a corporate level. Additionally, wearables generate massive amounts of new data. Corporate IT systems, including wireless infrastructures, at a connected plant will most certainly need to be modernized and scoped appropriately for efficient use.
Business justification and strategy
As enticing as new technology like smart glasses, SmartCaps and intelligent pumps can be, the ROI is what justifies the correct approach. Let’s look at some examples. As highlighted in Figure 2, real savings are achieved by providing workers a hands-free environment where information is consistently available to them in real time.
The intelligent pump example is a use case for mobile service workers. The savings captured by transforming a worker’s job out in the field to an assisted, remote operator are demonstrated in Figure 3. With remotely assisted, real-time predictive maintenance, service personnel can be at least two to three times more productive than their traditional counterparts.
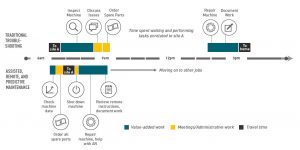
Figure 3: Savings for mobile service workers in the connected plant. Source: The Boston Consulting Group.
Conclusion
From drones to wearables and every application in between, the connected plant will become the new norm in the near future. Technology will play a major part as operators find novel ways to improve the bottom line with a shrinking workforce. Advances in hardware and sensor technologies will drive unforeseen gains. However, the big step change in the internet of energy will occur with the use of artificial intelligence to reduce costs, maximize efficiency and, most importantly, keep workers safe.
All IoT Agenda network contributors are responsible for the content and accuracy of their posts. Opinions are of the writers and do not necessarily convey the thoughts of IoT Agenda.