Reimagining the factory floor as a metaverse workplace
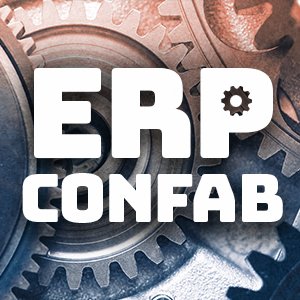
Plex CTO Jerry Foster explains how virtual reality technology and high-speed connectivity could allow factory line workers to do their jobs remotely from home as part of the metaverse.
Working on a factory floor seems to be almost the definition of a hands-on job. Buttons need to be pushed, levers pulled, equipment pushed into place and the unexpected handled in a flash.
But the reality is more complicated. Industrial machines are already largely controlled by computers, robots do much of the physical work and managers go looking for production efficiencies in the analytics apps that run on their smartphones. Industrial IoT sensors collect data that can go around the world almost as fast as it traverses a plant.
What if manufacturers could take these Industry 4.0 concepts further to create a virtual factory? The result could be a "metaverse workplace," where virtual reality (VR) technology, high-speed broadband connectivity and digital twins allow line workers to control factories from home.
That's the ambitious vision put forth by Jerry Foster, founder and CTO of Plex Systems, one of the original makers of multi-tenant SaaS ERP geared to manufacturers. In this podcast, Foster answered questions about the benefits and challenges of converting the plant floor into a virtual space in a metaverse environment and the steps needed to make it a reality.
Pandemic provided remote management test cases
Foster began by explaining how recent events demonstrated that remotely managed factories are possible, given the right foundation. He said cloud computing is a big part of that foundation, which is not surprising considering Plex's focus on cloud software, including ERP, a manufacturing execution system (MES) and applications for closely related functions like quality management and supply chain planning.
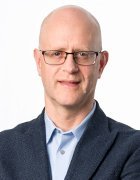
Foster told a story about a Plex customer that had to send most of its workers home during the pandemic. Half the plants used cloud-based software and the rest used on-premises software. The former continued running "as if nothing had happened," he said, but the plants with on-premises software struggled and corporate headquarters had little information about their status.
"In that scenario, they've sent all the workers home, except for the workers on the line because they still needed someone there pressing the buttons on the factory floor," Foster said. The practicality of a metaverse workplace for manufacturers becomes clear when you imagine sending the line workers home, too.
"They would go home, and they would put on their virtual reality goggles, and they would interact with a digital representation of their machine or their work center, which would send a signal in real time to its physical twin located dozens or hundreds of miles away," Foster said. "And it would actually build the part or do whatever thing that they were trying to do as if they were standing there in that actual physical location."
The benefits would be manifold: work-life balance, for one, as more people could work from home and cut back on tiring commutes. The talent pool would likely expand, a huge plus in an industry facing a shortage of skilled labor. "You're not restricted to just those who can commute," Foster said, as workers who can't drive or have physical disabilities would no longer be at a disadvantage.
VR technology could make it easier for manufacturers to deliver learning and development programs and train new hires remotely. It could also attract young workers turned off by factory work's dusty old -- and now generally inaccurate -- image. These digital natives might instead be attracted to the skill set needed to work in a virtual environment.
Foster was nevertheless clear-eyed about downsides. He acknowledged that shifting factory floors to the metaverse could actually worsen the skills gap. He said a purchasing officer who starts working from home is working the same way as in the office, but line workers must get used to VR goggles and visual representations over and above their normal job in the plant.
"There's definitely some training that has to happen there," Foster said. "My guess is it's going to take time to bridge that gap."
Steps to the next industrial revolution
To reach this metaverse nirvana, Foster said, a couple big things have to happen. Network connections must be more reliable so remote workers aren't thrown offline at critical moments, which is less likely in the typical factory with its internal network and backup power. That might mean upgrading facilities with 5G, the emerging high-speed cellular network.
Moving more operations to cloud-based software like the ERP and MES sold by Plex is the other foundational change. It might sound self-serving coming from Foster, but his point is that running industrial control systems in the cloud not only makes it possible for line workers to control machines from their browser, it gives managers global visibility into plants and access to the analytics they need to make decisions.
Because the broadband and cloud migrations are well underway, Foster guesses prototypes could be ready in five years.
In the meantime, he advised manufacturers to start moving operations like accounting to the cloud so employees can see how easy it is to work from home. Then look for economies of scale from automating the most basic, repetitive actions. Put robots and cobots in place and train workers to manage them remotely.
Other discussion topics include the following:
- manufacturing operations that are hard to control remotely;
- what Plex is doing to support the work-from-home vision; and
- how it uses APIs, software extensibility and middleware to accommodate manufacturers, which are typically thought to require customized, on-premises software.
To hear the podcast, click the link above.