What is SAP Planned Delivery Time (PDT)?
SAP Planned Delivery Time (PDT) is the estimated number of calendar days it takes for a company to receive an order from a vendor after a purchase order (PO) has been placed. PDT is used in SAP material requirements planning (MRP) and procurement scheduling to determine the last data a PO can be triggered and still have the purchase arrive on time.
Simply put, PDT estimates how much lead time a vendor needs to process a purchase order, fill the order and deliver it to the customer. The estimate is typically based on historical delivery data or contractual agreements.
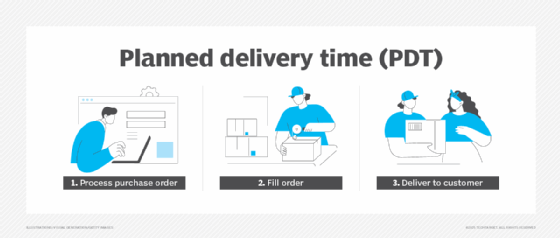
Planned delivery time is maintained in a dedicated data field and can be viewed in the purchasing view of the material primary record. In SAP, the material primary record serves as the single source of truth (SSoT) for all material-specific information required by different business functions.
Importance of SAP PDT
PDT is an important data field for material requirements planning in both SAP ERP Central Component (SAP ECC) and SAP S/4HANA ERP platforms. If the PDT is underestimated, the MRP engine will trigger the purchase order too late, and if the PDT is overestimated, materials might arrive much earlier than needed.
When PDT values are accurate and consistently maintained, stakeholders can anticipate delivery timelines more reliably and avoid overstock and out-of-stock situations that can affect revenue and profitability.
In lean production environments, accurate PDTs can also minimize the time procured goods need to be stored in a warehouse before use. This is especially important in just-in-time manufacturing, because excess inventory can tie up working capital, increase storage costs and raise the risk of materials becoming obsolete, damaged or expired before they are used.
How planned delivery time is calculated in SAP
SAP ECC and S/4HANA systems do not automatically calculate planned delivery times. Instead, organizations guide the manual entry of accurate PDT values by analyzing historical procurement performance data, such as the time between purchase order creation and goods receipt (GR).
In most cases, a procurement analyst or supply chain planner will analyze the vendor's past procurement performance and/or refer to the vendor's service-level agreement (SLA) to determine the correct value for a PDT. Once the PDT has been determined, the primary data administrator responsible for maintaining material primary data will enter the PDT value in the material primary record.
If a specific lead time applies to a particular vendor-material combination, PDT can also be entered in the purchasing info record. This will override the value in the material primary for that vendor.
To make it easier to calculate PDT from historical data, retail organizations using SAP Forecasting and Replenishment (SAP F&R) can use a built-in function called Workload Planned Delivery Time Calculation (WPTDC). This function will analyze past procurement data and suggest PDTs automatically. The suggestions can then be reviewed by an authorized user and manually applied to the purchasing info record or material master record if desired.
SAP PDT and calendar days
Although SAP PDT is entered as a single value, it often reflects multiple real-world factors in supply chain management (SCM). In both ECC and S/4HANA, the PDT is expressed in calendar days that run continuously without interruption, while other lead time elements like purchase processing time and goods receipt time are measured in business days that exclude weekends and public holidays. This hybrid approach ensures more realistic scheduling and fewer planning errors by aligning vendor lead times with internal processing times.
By treating external and internal timeframes differently, SAP reduces the following risks:
- Underestimating lead times.
- Overpromising delivery dates.
- Creating schedule issues that can cause stockouts or excess inventory.
Using PDT for time-based planning
Time-based planning is a procurement strategy that uses a planning calendar to schedule new orders on predefined dates instead of reacting to changes in demand or stock levels. Time-based planning might also be referred to as time-phased planning.
PDTs play a supporting role in time-based planning by helping to determine the last possible date a purchase order can be triggered and still have the order arrive on time. Essentially, the material requirements planning engine treats the PDT as the minimum lead time needed between order creation and goods receipt to ensure on-time delivery.
When this procurement strategy is being used, the SAP ERP platform will only run MRP and generate procurement proposals on specific days that are identified in the planning calendar. Typically, the dates for time-based planning are aligned with the vendor's delivery schedule or available shipping windows.
Earliest availability date vs. planned delivery time
In SAP, the earliest availability date (EAD) refers to the soonest date that ordered materials can be made ready for use based on current stock, lead times and confirmed supply in transit. Here's how it's typically calculated for externally procured materials:
Earliest availability date = order placement date + planned delivery time + goods receipt processing time
When a new order is created in SAP, the system calculates the earliest availability date and compares it with the desired delivery date. Unlike PDT values, which are often determined by a human being, earliest availability dates are determined dynamically during MRP runs or available-to-promise (ATP) checks. In SAP, an ATP check dynamically assesses supply against demand at the time of order entry.
To identify the earliest availability date as accurately as possible, SAP might also consider other relevant lead times such as the following:
- Current stock and open orders. The confirmed inventory that is already on hand or is currently in transit.
- Purchasing or production processing time. The time needed to issue a PO or manufacture the material in-house.
- Transportation or shipping lead times. The time it takes to move the material between locations.
It should be noted that manually changing the order placement date in SAP can directly affect how the earliest availability date is calculated. This is because manual changes can bypass the system's dynamic scheduling logic and prevent it from factoring in planned delivery time and other lead time components. In some cases, this might trigger a rescheduling process that shifts the earliest availability date to a past date, which will create inconsistencies in MRP runs and availability checks. SAP will trigger an alert which the user can see in the alert monitor, but if the user happens to miss or ignore the alert it can lead to scheduling and delivery problems.
Replenishment lead time vs. planned delivery time
Replenishment lead time (RLT) is the total amount of time it will take to restock a material and make it available in inventory. PDT can be thought of as a subset of RLT that estimates the minimum number of calendar days the vendor will need to deliver an order after the purchase order is placed.
RLT can be calculated either manually or automatically depending on the SAP module in use and whether historical data is available for automated analysis. In standard SAP ECC and S/4HANA deployments, the components that make up the RLT are calculated and entered manually in the material primary record. The ERP system then adds individual lead time components together to determine the overall replenishment lead time for planning purposes.
SAP uses RLT in availability checks, available-to-promise logic and planning strategies that are designed to ensure realistic scheduling and delivery confirmations.
Replenishment lead time is also a key feature of SAP F&R, an optional software module SAP created for retail organizations.
PDT and SAP F&R
SAP F&R is an optional software module designed for high-volume retail businesses. It extends the functionality of SAP ECC or SAP S/4HANA by providing advanced features for demand forecasting and automated replenishment planning.
Technically, SAP F&R enhances inventory management by modeling lead times, sales patterns and seasonal demand behavior. The module's predictive capabilities enable businesses to reduce surplus stock, avoid stockouts, automate replenishment activities and minimize the total cost of ownership (TCO) associated with supply chain operations.
F&R replenishment lead times can be automatically calculated using historical procurement and supply chain data. The RLTs can then be reviewed by authorized users before being applied, and values can be periodically updated in the material primary to reflect the vendor's recent lead times.
Backward scheduling and forward scheduling for external procurement with PDT
SAP ECC and SAP S/4HANA use backward scheduling for standard MRP runs and procurement scheduling. Backward scheduling subtracts the planned delivery time and goods receipt processing time from the requested delivery date to determine the last possible date for initiating procurement.
If backward scheduling is not feasible, SAP will switch to forward scheduling. Forward scheduling starts from the current date and adds lead times to determine the earliest possible fulfillment date.
The ability to switch helps ensure realistic delivery promises and prevents unrealistic scheduling. In both scheduling modes, PDT is used to model the vendor's delivery lead time and estimate the number of calendar days needed between purchase order creation and goods delivery.
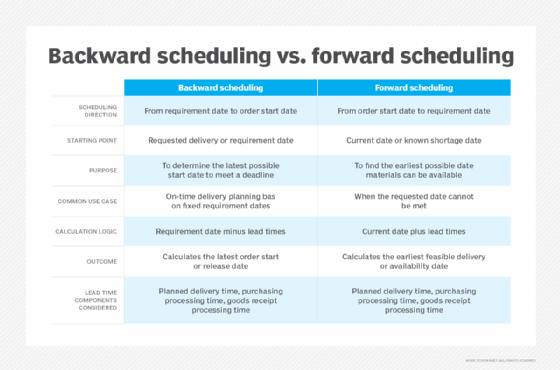
SAP is encouraging customers to move to S/4HANA because it will stop mainstream support for SAP ECC on Dec. 31, 2027. Learn about the advantages and challenges of migrating to S/4HANA in this comprehensive guide.