12 notable ERP implementation failures and why they failed
ERP consultants share their analysis and takeaways from such spectacular ERP failures as Nike, National Grid, Revlon and MillerCoors and give advice on avoiding ERP pitfalls.
There are a lot of ways ERP systems can fail. Many businesses rush into rolling out new functions without careful consideration of details -- or knowing the common reasons for ERP implementation failure.
"It takes time, dedicated training and adequate management for ERP to flourish as a proficient tool within your business," said Jenny Chua, business development manager at The World Management, an ERP consultancy in Singapore.
John Belden, chief of strategy and research at Boston-based UpperEdge, an IT negotiations consultancy, commonly sees three key characteristics of these projects that often contribute to ERP implementation failure:
- ERP implementations are often 2 to 10 times bigger than previous projects.
- They are transformational, which means there are winners and losers in the organization because of the digital transformation enabled by the implementation.
- They are generational, which means an organization might not have done anything comparable in 10 to 15 years.
"A program will have problems when enterprises don't recognize these issues and try and mitigate these risks," Belden said.
These 12 well-publicized cases of ERP implementation failure illustrate some of the main reasons why these operations fail and how to avoid them.
1. Nike's unrealistic goals
Nike thought it could "Just Do It" when it embarked on a $400 million upgrade of its ERP system in 2000. But the new system resulted in $100 million in lost sales and a 20% drop in stock price when it couldn't fulfill orders for Air Jordan footwear.
"Nike was overly optimistic in their goals, and they failed to verify business process met operational needs before deploying the system," said Alex Sharpe, founder of Sharpe Management Consulting, based in Bridgewater, N.J.
The lesson: It's important to set realistic goals in the implementation plan, especially regarding ERP functionality and project schedules. Sharpe also recommends defining operational and business requirements early on and keeping them in mind when developing systems.
"Ensure you take enough time to test the system for any kinks that need to be ironed out before putting your system into production," he said.
2. MillerCoors' hiring the wrong people for the job
MillerCoors, which changed its name to Molson Coors Beverage Co. in January 2020, embarked on an ambitious plan to consolidate its financials on a single ERP system to reduce costs and improve operational efficiency. In 2014, it hired HCL Technologies to implement the project, which was stalled by numerous defects. MillerCoors ended up suing HCL for $100 million, and the lawsuit was finally resolved in 2018.
Deepak Lalwani, principal and management consultant at Deepak Lalwani & Associates, an IT consultancy, said the problem arose because the planning and architectural phases were not given adequate consideration. In addition, many critical defects and other additional problems were identified but not fixed.
HCL's core competency was generally regarded as implementation, not planning and architecture.
The lesson: Ensure you have the right ERP expertise for the particular project. "IT is often the toughest and the most expensive part of integrating multiple companies, and they rushed through the planning and architecture phase only to get hurt by it later," Lalwani said.
3. Revlon's underestimation of operational impact
Revlon attempted to integrate its ERP processes across business units after a merger with Elizabeth Arden in 2016. The new system failed spectacularly after it went live in 2018, resulting in a loss of $64 million in sales, a 6.4% loss in stock price and an investor lawsuit.
A key issue was that Revlon had attempted to consolidate Microsoft and Oracle systems on a new SAP implementation but lacked hands-on experience with SAP. It also decided to go live without making sure the ERP business processes would work as intended.
"Rolling out a system that does not meet operational needs and requirements often leads to adverse business impacts," Lalwani said.
The lesson: Mind both the operational and business sides of the ERP equation.
4. National Grid's lack of disaster testing
National Grid's ERP implementation was essentially blown away by Hurricane Sandy in 2012 when the utility attempted to consolidate its U.S. operations on a common SAP system. Ultimately, the project took two years to clean up, at a cost of $585 million.
The parent company had successfully worked with the Wipro consulting firm on a similar ERP consolidation in Europe, but the ERP project team struggled with major differences in the regulatory environments in the U.S. Wipro suggested the SAP ERP project was ready to go live based on test results, but the actual system did not hold up under the increased workload. Emergency business processes were required to repair the electric grid after the hurricane, which involved special procedures for bringing in workers and materials from other utilities for the extensive repairs.
Belden said the implementation team had focused on "happy path" testing, which involved testing functions under ideal circumstances, but there had been insufficient testing of the system in emergency scenarios. National Grid decided to go live as the hurricane was making its way up the coast.
The lesson: It is vital to assess all the factors that can affect readiness before going live with a large ERP implementation.
5. Waste Management's failure to verify vendor claims
Waste Management ran into some major snags when it attempted a massive SAP installation in 2005. After numerous problems and delays, the company ended up in a $500 million lawsuit against SAP that was eventually settled out of court.
SAP had suggested Waste Management could achieve $106 million to $220 million in annual benefits from a consolidated ERP system that could be implemented in 18 months.
Lalwani said one big problem was Waste Management's failure to verify SAP's claims before making an executive decision. The company quickly discovered there were significant gaps between what was promised and what was delivered in the software.
The lesson: Verify vendor claims with internal business and technical teams. "Performing a proof of concept on critical functionality … can reduce significant risk," Lalwani said.
6. The University of Washington struggles to pay vendors
The University of Washington initially planned a migration to a cloud-based finance platform in 2022 as part of its $340 million five-year UW Finance Transformation project. The rollout was delayed by a year but finally started making some headway in 2023. Many core processes for taking payments and paying staff made it into the new system. However, payments to vendors and funneling research grants were massively delayed.
Gaurav Joshi, a director at global management and technology consulting firm AArete, based in Chicago, has seen many instances where large ERP systems designed to enhance financial performance ended up creating disruption for the HR, procurement and accounts payable teams, as well as the vendor base. As a result, an organization might not realize the expected efficiency and data visibility benefits of the project, as it can sometimes spend multiple years battling bugs, organizational tension and operational disruption.
Proactive change management should start with recognizing and acknowledging that an ERP upgrade is one of the most complex projects the organization will undertake. It also requires involvement from key decision-makers spanning all important functions and user groups.
It is also important to consider all the stakeholders affected by the project. This includes not just business and functional users, but also the larger ecosystem that encompasses customers and vendors.
The lesson: "Keeping all stakeholders abreast of the impacts the project will have on their day-to-day jobs is critical," Joshi said.
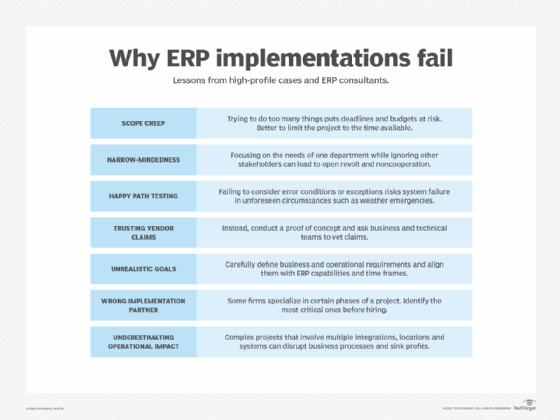
7. Invacare's ERP solution catches a cold
Medical device manufacturer Invacare's ERP project faced a key setback in rolling out a major SAP upgrade in 2021. Unfortunately, the company had to pay a monthly maintenance fee to the system integrator as the project dragged on into 2022, and the fed-up board went shopping for a new CEO in August 2022.
"ERP implementations are one of the most resource-intensive projects a company can pursue; budget and timeline mismanagement can derail an ERP project or stop it altogether," Joshi said.
The software and support vendors a company chooses can make all the difference. Joshi has found it important to conduct a request for proposal process that includes a comparative bid analysis, vendor demos and a scorecard filled in by key stakeholders.
The lesson: It's important to accurately estimate the total cost of ownership, have a timeline that considers all services and partners, and develop a plan to avoid cost overruns due to change orders or delays.
8. PG&E's production data leak
In 2016, Pacific Gas and Electric faced a significant security breach when a third-party vendor hired to create a new asset management platform copied live PG&E data to its own network without implementing necessary security measures during Oracle ERP testing. This led to more than 30,000 data items being online and accessible for nearly 70 days.
A white-hat security researcher alerted PG&E to the breach, prompting the utility company to initiate recovery efforts. These efforts included substantial costs and a nearly $3 million fine. In addition to financial expenses, PG&E's reputation and customer confidence in how the utility manages sensitive data were damaged.
The lesson: Ensure project teams possess the required technical expertise, and use a dedicated testing environment that doesn't handle live data.
9. Cover Oregon's outsized project
Bigger projects tend to put an organization in a position where it is not prepared for the volume and magnitude of decisions required. As a result, overwhelmed teams end up piling on one bad decision after another.
Belden said a classic example was the 2012 attempt by the state online healthcare marketplace, Cover Oregon, to simultaneously implement Obamacare and replace its supporting transaction processing systems. It ultimately spent more than $300 million and was unable to process a single insurance application through the exchange.
"They created a scenario where the project got so enormous, they could not meet the due dates," Belden said, or make the decisions that were required. Problems were exacerbated by the need to meet the hard deadline imposed by Obamacare. Belden said he believes the project would have worked out if Cover Oregon had kept the ERP project smaller and restricted it to what would have been required for Obamacare.
The lesson: Limit the scope of the ERP project to the appropriate time frame.
10. Israel Chemical Limited's narrow focus
Generational problems can occur when no one on the program management team understands where the problems are.
"They may have prior experience, but it was 10 to 15 years ago and the people who learned the lessons are somewhere else in the organization or have moved on," Belden said.
A good example is Israel Chemical Limited's (ICL) failed SAP ERP implementation in 2014. The project cost ballooned from $120 million to more than $500 million. Ultimately, ICL's CEO resigned, and the entire implementation was cancelled.
The CEO had assigned the project to a relatively new person in the CFO's office, according to Belden. This project lead was primarily focused on making sure financials were properly incorporated into the ERP project, rather than also considering the needs of the manufacturing and supply chain sides of the business. Employees in the first factory revolted after they had the new system imposed upon them.
"They got more focused on financial integrity rather than operational integrity," Belden said.
The lesson: Focus on all users of the proposed ERP implementation and not just one part of the business.
11. Ranpak delayed by unexpected global conflict
Packaging firm Ranpak rolled out a new ERP in January 2022 to coincide with the new year. It also happened to occur just before the Russian attack on Ukraine, which has strained supply chains and added further complexity to cost structures. As a result, sales dropped and shipping times increased. All these factors combined to slow ERP implementation and increase costs. The company finally started to achieve some success after working through the resulting, additional ERP implementation challenges much later than expected.
"While certain risks can never be predicted, a good ERP implementation project plan always has some flexibility built into it," Joshi said.
For example, Joshi said AArete worked with a client experiencing rapid growth that expected accelerated turnaround times for its ERP implementations, so it developed contingency plans in case any acquisitions were announced during the migration -- which occurred twice. This planning streamlined training for the acquired company's functional users, incorporated required business needs and data sets, and found compromises where necessary.
The lesson: A substantial ERP implementation can take time, so it is important to identify and plan for contingencies that might affect the rollout.
12. Mission Produce underestimates supply chain needs
In 2022, Mission Produce upgraded its enterprise software system to improve supply chain management and efficiency. When the system went live, there were order processing delays, inventory inaccuracies and communication issues among business units, resulting in missed delivery deadlines and financial losses. By failing to understand the needs of its global partners, Mission Produce did not adequately validate requirements and underestimated its ERP timeline. Other contributing factors were a lack of employee training in the new system and no individual or team heading the project.
The lesson: It's important to include all stakeholders in the requirements gathering phase. Be realistic with the ERP project timeline, implement strong project management practices and conduct testing to catch any issues before the system goes live.
How to avoid ERP implementation failures
The following are some common factors to consider during an ERP implementation:
- Select a knowledgeable vendor. Evaluate ERP vendors with a history of successful software implementations.
- Get feedback from all stakeholders and build the migration team. To enhance project success, get feedback from all departments, ensure key migration team roles are filled and install a knowledgeable project manager.
- Control project costs. Ensure staff resources are available and finalize what features and capabilities are required for the project. Staffing changes and last-minute customizations can lead to scope creep that drives up costs.
- Establish a realistic timeline. Larger organizations consolidating multiple legacy systems will need to extend their migration timeline.
- Prioritize change management. Map current business processes to the new ERP system to smooth the transition and training.
- Focus on system integration. The newly selected ERP system should integrate as seamlessly as possible with internal systems and any other tools that might be implemented.
- Ensure data quality. Most organizations have data stored in different formats and owned by different stakeholders. All data for the new ERP database should be accurate and consistent before it's migrated.
Editor's note: This article was updated in June 2025 to include additional failed ERP projects and to improve the reader experience.
George Lawton is a journalist based in London. Over the last 30 years he has written more than 3,000 stories about computers, communications, knowledge management, business, health and other areas that interest him.