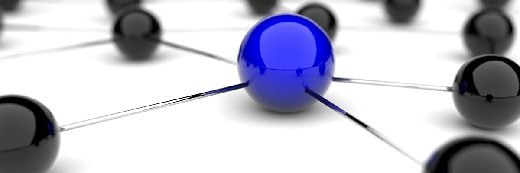
pixeltrap - Fotolia
How material requirements planning can lead to more inventory
It seems counterintuitive, but inventory can actually increase after implementing an MRP system. Here are some reasons why it's so hard to zero out the excess in the supply chain.
Most companies, when they buy and install a new MRP or ERP system, justify it, to a great extent, on the expectation that they will be able to reduce inventory without increasing shortages. However, it doesn't usually work out that way. Most companies will experience an increase in inventory following an implementation, which doesn't improve until they take some additional steps. Here's why inventory increases.
Material requirements planning (MRP) is the main calculation engine that forms the heart of ERP for manufacturers. Using demand and the bill of materials, MRP calculates the items (materials) that are needed every day, checks projected availability from inventory records and determines where shortages are expected. Finally, MRP creates the recommended replenishment (purchase and production) orders needed to eliminate the shortages.
Material requirements planning is inherently an Inventory optimization system, meaning that its recommendations will result in the proper (that is, minimum) amount of inventory required to avoid shortages, given the information and conditions. Theoretically, companies moving to MRP or implementing a new version of MRP should experience lower overall inventory levels, while at the same time, improving availability (thus preventing shortages). Many do see these results, but not right away, and often not to the extent that they might have hoped.
How material requirements planning affects inventory
Most often, MRP does improve company performance by reducing shortages. But inventory almost always increases. This is because the system now anticipates the need before the shortage occurs, and the recommendation will bring in the needed inventory "just in time" to avoid the shortage.
The sad reality is that the system will often bring in too much inventory too soon (learn more about this below), while the company still holds quantities of unneeded inventory left over from before MRP was planning the right quantities of the right items at the right time. It will take some time to use up the extra inventory and recognize what is truly surplus -- unneeded -- and dispose of it or write it off.
Why does material requirements planning bring in too much inventory too soon? Once the calculation identifies the exact quantity needed and the date it is needed by, the next two steps in the calculation create the recommended order size and timing.
Since it is often uneconomical to make or buy a small amount or odd quantity of a particular item every day, the system uses lot-sizing rules (also called order policies) to come up with the optimum recommendation. Lot sizing can be as simple as "always order 100 at a time" or can be a sophisticated calculation that balances the cost of multiple orders compared to the cost of holding more inventory from fewer orders and, thus, having a longer holding period for stock between orders -- a technique called economic order quantity.
Any lot sizing other than getting exactly what's needed when it's needed (called "discrete" or "lot-for-lot") will result in some amount of inventory. New MRP implementations tend to use general rules for lot sizing because it's just too hard to thoroughly analyze and determine the best lot-sizing rule for each item. The result is a buildup of extra inventory.
Remember, too, that MRP cannot create a perfect plan because the planning parameters are set up based on normal or average conditions, and the real world is seldom stable and predictable. Planners manage variability through the use of compensating factors like safety stock, shrinkage and yield factors. Each of these compensating factors (control fields in the item planning record) will generate additional inventory to boost the chances of having ample supplies when disruptions occur or schedules change at the last minute. This is another major source of inventory buildup when moving to material requirements planning.
The other source of extra inventory results from a different type of compensating factor: padded lead times used in the planning process. Whatever a vendor promises for delivery lead time after receipt of an order, most buyer/planners are apt to add a bit of buffer to protect the plan from the possibility of a late delivery. If the vendor quotes five days, for example, the planner might enter a lead time of eight days or more in the planning file. When MRP recognizes the need for the purchased item on a given date, it will signal the buyer to release the order eight days earlier. If the vendor delivers in the previously quoted five days, the stock will arrive three days before it is needed and will be part of the inventory for those three days.
Even though MRP is, by its very nature, a just-in-time calculation that should, theoretically, result in zero inventory, in the real world, we add planning parameters and compensating factors to account for economic considerations, variability and schedule changes. All of these things add inventory. Meanwhile, in a new MRP situation, we start out with some quantity of extra inventory left over from the pre-MRP (or ineffective MRP) days that will take some time to work through. Added together, we often find ourselves with a disappointing and aggravating increase in inventory shortly after implementing a new MRP system.
The situation is not hopeless, however. Inventory can be reduced without damaging availability and customer service. It takes an extra effort, though, beyond the initial implementation to understand and properly use the controls and factors that drive the MRP process.
Next up: A discussion of how to reduce inventory with MRP.