MRP vs. ERP: Understand the differences and similarities
Did you know today's ERP systems evolved from yesterday's MRP systems? Learn the differences, including functions, applications and benefits -- and how they work together.
Understanding the difference between ERP and material requirements planning is important to getting the most out of these systems.
While ERP evolved from MRP, which was focused on calculating material requirements for manufacturing and still forms the backbone of most ERP systems, the two are very different and operate in connected yet nonetheless distinct realms.
What is ERP?
ERP -- enterprise resource planning -- can be described as an integrated set of software applications that address the needs of a business enterprise. Two aspects of that definition are the critical differentiators.
First, ERP is comprehensive, with applications that address all the operational and administrative functions of the business, from everyday accounting, billing and finance to sales and customer service, warehousing and distribution, production and procurement, field service and more.
The second aspect is integration. Besides having applications that are integrated with each other, ERP systems are built around a single database that holds all the data from the entire business. In some cases, the data comes from remote plants and warehouses, partner factories and distribution centers, contract suppliers and service providers, and other parts of the extended enterprise.
History of MRP, MRP II and ERP
The term MRP originally referred to material requirements planning, a very specific software application that calculates the materials needed to manufacture a product, including each component or material, its quantity and when it is needed. This was useful, of course, and a major breakthrough in the history of software as a business tool.
But MRP only does the one thing: calculate the basic plan. Additional software was needed to help apply the material plan in actual operations, and in doing so, collect information that will allow MRP to track progress and "close the loop" as it develops new and updated plans.
The first of the additional integrated applications included inventory management, production activity tracking (shop floor scheduling and control), purchasing, and customer order management (to identify the production needs and requirements), which in turn was coordinated with inventory management to track shipments and inventory depletion. As software developers extended the application set to these other areas of the business, MRP became a lot more than the basic planning calculator, so a new descriptor was needed. Enter manufacturing resource planning (MRP II).
The new name unfortunately had the same initials as the material calculator, so the Roman numeral was added, and MRP II became the accepted name for the software suite.
By the early 1990s, MRP II had become broader and more comprehensive to the point that many non-manufacturing companies found they could implement it without the manufacturing planning and operations functions. But some wouldn't even consider MRP II because they weren't manufacturers.
A new name was needed. That's when the term enterprise resource planning (ERP) entered the picture. The initial definition of ERP also stipulated some technical requirements, such as a relational database and client/server architecture, which may have been unnecessary detail at the time and have since become either standard practice or obsolete. Nevertheless, ERP is now the accepted term for the comprehensive, integrated software suite for business management.
It is important to note that the planning function in most ERP systems is based on MRP or a derivative, even though many software developers try to hide that fact because MRP is old technology with known limitations. The new systems have evolved to overcome those limitations in various ways, but the basic MRP approach is still at the root of what they do, just as algebra still relies on basic addition, subtraction, multiplication and division.
One more point: The term MRP II has mostly disappeared from use and anyone using the term MRP is most likely referring to what was once called MRP II -- the software suite with MRP in the center and support applications integrated around it. If you are looking at MRP software, you are almost certainly looking at what used to be called MRP II and could rightly be called ERP-lite: a less sophisticated, less comprehensive version of ERP.
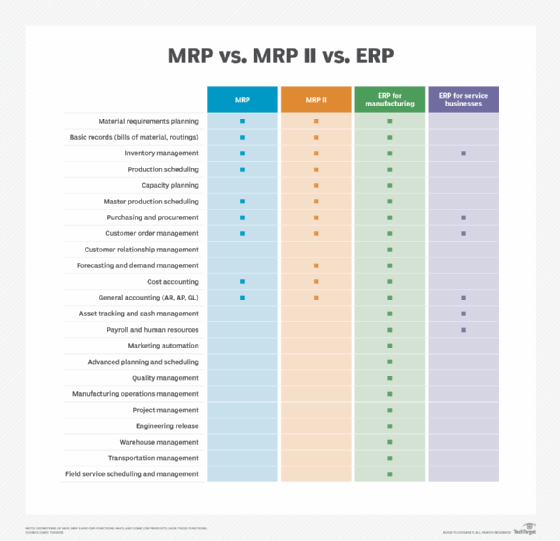
MRP vs. ERP: Key differences
As its name suggests, MRP is focused on manufacturing planning and scheduling, as well as related functions like customer order management, inventory management, purchasing and accounting. In contrast, ERP encompasses a much wider range of business functions, such as customer relationship management, financial management, HR, sophisticated business planning capabilities and business intelligence (BI).
ERP is an integrated software suite that manages the majority of company information, while MRP in the traditional sense is one application, or module, in that suite. MRP, in its modern definition, is MRP plus the supporting applications for basic manufacturing operations and accounting. Manufacturers can go either way, depending on their needs. Non-manufacturers should be interested in ERP and have little use for MRP.
Today's ERP -- and tomorrow's
It should be apparent by now that new tools and technologies are continuously being applied to ERP suites, while MRP developers are focused on maintaining and enhancing existing functionality using proven technology. Limited sophistication can be considered a benefit to smaller companies without a lot of technical resources in-house. MRP can be simpler and quicker to implement at lower cost, as well as easier to maintain and support.
Recent developments in the ERP world include advanced executive information tools (including BI, data mining and predictive analytics), sophisticated planning tools using AI, machine learning and simulation; applying these same tools to global supply chain monitoring and management with industrial IoT sensors and location-aware tracking and monitoring devices; and cloud-based systems for global access, partner and resource connectivity, unlimited scalability and industrial-grade security.
Many modern ERP systems today are developed as cloud-based applications and nearly all offer cloud deployment as an option. Cloud ERP is considered to be the most flexible, easiest to implement and most scalable type of ERP. With cloud ERP, the size of the database, number of users and processing load are infinitely scalable without additional capital outlay or outdated or unneeded equipment to dispose of.
Features of ERP systems
ERP systems generally consist of modular applications that each address a specific business process. Modularity is a particular strength of these systems because it allows organizations to tailor a system to fit their needs by implementing only the necessary applications or modules. Later, as needs change, modules can be added, or removed if they're no longer needed.
Most ERP systems have or will eventually have additional modules that make the system more complete. These can include human capital management (HCM), supply chain planning and management, and support for business functions that not every company needs, such as field service management, deep quality management capabilities, as well as advanced and finite scheduling.
The ability to mix and match these optional modules provides a way to tailor the system to fit specific industries like food and beverage, industrial equipment, electronics, consumer goods or process manufacturing, as well as non-manufacturing, such as retail, distribution, business or consumer services, schools and many more. An accounting or consulting firm, for example, would not need material planning, production scheduling or inventory management but would need schedule (calendar) management, document management, service billing, HCM and general accounting.
Benefits of MRP
Keeping in mind that MRP is a specific set of functions in an ERP suite, MRP is the backbone of the system and the thing that brings the entire manufacturing business together in a coordinated effort toward the overall goal of delivering quality products to customers on time. MRP (the module), in conjunction with master scheduling, turns the demand plan (forecast and orders) into specific tasks for production, procurement, resource management and the rest of the enterprise. The rest of the system then tracks and manages the execution of those tasks.
As such, MRP directly contributes to the following:
- More efficient production and supply chain management.
- Better customer service.
- More effective use of available resources.
- Cost savings.
Benefits of ERP
The main purpose of ERP is the following:
- Collect and manage information.
- Make it available where needed across the enterprise.
- Perform various calculations and analyses that support decision-making.
Because the software basically models the operation of the enterprise, it can offer additional insight into cause-and-effect relationships between activities and decisions across functional areas of the business, enabling more effective and efficient business operations.
It has been said that information is power, and in today's business world, managing and exploiting information is critical. ERP encompasses the entire extended enterprise, bringing the various functions together to coordinate their activities and decisions and keep them focused on achieving the ultimate purpose of the enterprise, which is to generate a profit by delivering the goods and services customers expect in the most economical way.
The real question is not, what are the benefits of ERP? Rather, it is, how can a modern company ever expect to operate effectively without control over its information and the decision-support functions provided by ERP?
Dave Turbide is a former contributor to SearchERP.