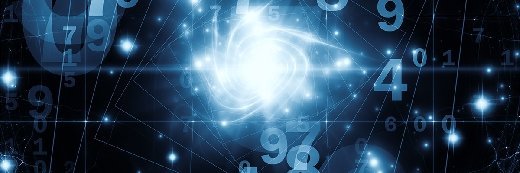
agsandrew - Fotolia
How manufacturers can use an MRP system to reduce inventory
By focusing on compensating factors such as safety stock and shrinkage, you can counteract the tendency of an MRP system to increase inventory, especially in the beginning.
Most companies expect a reduction in inventory along with fewer shortages when they implement a material requirements planning (MRP) system. This win-win result is certainly achievable and is the measure of a successful MRP system implementation.
What most companies experience in the first few months of operation under MRP, however, is more of a win-lose: fewer shortages but higher inventory. The reasons why inventory can go up are covered in a companion article. This article addresses the second part of MRP implementation -- the part that brings inventory down.
The MRP system is the calculation engine within ERP that uses product demand, bills of materials and inventory information to recommend the replenishment (purchase and production) orders that are needed to eliminate the shortages. MRP is focused on inventory optimization, i.e., determining the right amount of inventory to do the job. The planned amount of inventory is greater than zero because of economic considerations (lot sizing) and additional quantities that have to be planned to reduce the risk of stock-outs caused by variability -- schedule changes, late deliveries, unexpected scrap, data errors and the like. Companies must include compensating factors in the MRP setup to accommodate variability and reduce the shortages that would otherwise occur.
The extra inventory that the system plans for economic and variability reasons adds to the extra stocks that existed before the MRP system, which results in an overall increase in inventory that taints the benefits of having the system. Therefore, companies must take additional steps to bring those inventories back in control.
Compensating factors are main inventory levers in MRP system
The simple solution for reducing inventory in MRP is to reduce the compensating factors: safety stock, shrinkage, yield and scrap allowance, and safety lead times. But to just reduce the factors will increase the risk of shortages. The real solution is to identify and reduce the sources of variability and risk, reduce those, then lower the compensating factors accordingly.
Each compensating factor is intended to address a particular kind of variability or risk. Lower the variability and you can lower its compensating factor. Let's look at safety stock as an example. Safety stock is the commonly used factor; often the only one when users don't understand all the options and what they are for. Nevertheless, safety stock compensates for variability in demand (from forecast error for finished goods) and also for variation in supply -- such occurrences as late delivery from the plant or from a vendor, inventory surprises arising from inaccurate inventory records, or unreported usage or scrap, and so on.
Safety stock is commonly set using some rule of thumb or, at best, rules and policies for certain groupings of items, such as high volume vs. low volume, or raw materials vs. fabricated parts. The groupings represent the amount of risk to be addressed.
There are two general approaches to studying the risk vs. compensation relationship: analytical and empirical. In the first approach, you study past performance to identify any patterns or trends in variability that result in higher-than-expected demand or lower-than expected supply (and that would have led to a shortage if safety stock was not in place). From that information, you can calculate the proper amount of safety stock for an item or a group of items to deliver an acceptable risk of stock-out.
In the empirical approach, you check the records to identify the actual number of shortages that have occurred with the current amount of safety stock. Then you remove a modest amount of safety stock and track shortages. If the number of shortages has not increased, you can maintain that amount of safety stock from that point forward. You may want to repeat the experiment to determine the minimum amount of safety stock that yields an acceptable service level.
The same approaches can be applied to the other compensating factors:
- Shrinkage compensates for losses not related to production (loss, damage or expiration in the warehouse, for example). Shrinkage can also be used to make up for inventory accuracy errors, along with safety stock. Inventory accuracy is one of the biggest sources of variability in most companies and one that can be directly addressed and improved with cycle counting and enhanced discipline in handling and reporting inventory movement.
- Yield and scrap factors apply to in-production losses. If the process ordinarily results in losses, either component losses or end-item loss, there are fields in your system to recognize and compensate for additional component requirements and/or additional production-start quantities so you'll have the required quantity at the end of production. Disciplined feedback (inventory reporting and shop activity reporting) and a review of actual experience will help you keep these factors on target.
- There's no easy fix for schedule changes that are made inside of lead time, and no specific compensating factor other than safety stock. Companies are well advised to establish and respect a frozen zone in the master schedule and communicate clearly to sales and customer service personnel that promising customer shipment beyond the forecasted amount and within the normal lead time for a product causes disruption and destroys profit.
Additional inventory reductions are available when lead times are reduced. Shorter lead times offer fewer opportunities for unexpected changes (variability) and, therefore, justify a lowering of compensating factors that will result in lower inventory. Shorter lead times also allow you to hold less inventory while providing needed availability, but this relationship is not tied directly to MRP customer service requirements and is not part of the inventory buildup that can happen with new MRP system implementations.