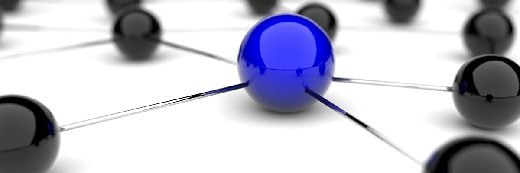
pixeltrap - Fotolia
Can MRP be successful without 98 percent inventory accuracy?
Effective MRP requires prioritizing inventory accuracy and true troubleshooting over a reliance on safety stock and other compensating factors.
The old rule of thumb says that material requirements planning (MRP) requires an inventory accuracy of 98%. Although this level of accuracy is a worthy goal, there's nothing magic about it other than it is quite stringent -- but also achievable.
A company's MRP can be successful with less accurate inventory records, but the higher the accuracy, the better the results. And by results, I mean the ability to achieve high levels of availability with less inventory on hand. Lower accuracy levels either reduce availability (more stockouts) or require more inventory to achieve the availability level, or both.
Obviously, high inventory accuracy is important. Also important are bill-of-material accuracy, stable schedules and avoiding late changes that disrupt ongoing activities and negate previously developed plans and schedules.
MRP systems are designed to accommodate the inevitable limitations that manufacturers deal with every day, including record inaccuracy, late deliveries and unexpected scrap. Your system has provisions for compensating factors built into the database that the MRP calculation uses to make up for these challenges.
Safety stock is the compensating factor with which most people are familiar. It drives extra inventory into the system so that small disruptions don't cause a shortage. Having a modest amount of safety stock is a prudent operating strategy. Too much safety stock (more than necessary to overcome those small errors) provides no benefit and increases inventory balance -- something most companies try to avoid.
Other compensating factors include shrinkage allowance to cover for losses outside of production (e.g., theft, damage in the warehouse); scrap factor or yield factor for losses that occur during production; "safety" lead time -- giving suppliers or the plant a falsely early due date so a late completion or delivery does not cause a shortage; and adjusted bill-of-material quantity per to compensate for component losses or component quality problems.
Remember that any of these compensating factors drive higher inventory levels -- a necessary cost of business to prevent disruptions caused by shortages. Compensating factors should be used wisely and only enough to achieve that objective. Performance improvement and inventory reduction result from identifying the underlying problem (e.g., late delivery, record inaccuracy), taking action to improve the situation, and then reducing the compensating factor in the planning system so that the compensating inventory is reduced.