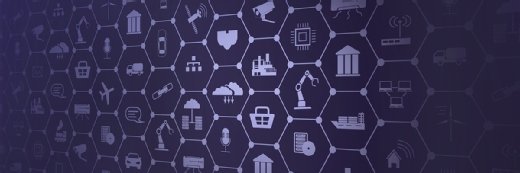
Getty Images/iStockphoto
MRP vs. MPS: What are the differences?
Learn about MRP vs. MPS, including how each focuses on different aspects of the manufacturing process but can help manufacturers in a variety of ways.
Manufacturers rely on carefully controlled production processes to create the finished goods that they sell to wholesalers, retailers and other customers. Two of the most important aspects of manufacturing are the master production schedule and material requirements planning, and although they are closely linked, some important differences exist between the two.
Manufacturers use both to optimize how they design and produce their products, so understanding the differences between MRP and MPS enables manufacturers to potentially improve their production, minimize waste and increase profit margins.
Here's more about MRP vs. MPS.
What is dependent and independent demand?
Two important concepts to understand when discussing MRP and MPS are independent demand and dependent demand.
Independent demand, also known as direct demand, is the demand for a finished product. Independent demand is predicted by looking at sales forecasts and orders, among other data. For example, a retailer selling a television and ordering a new one from a manufacturer creates independent demand for that TV.
Dependent demand is the need for the components that make up a finished product. For a TV, the dependent demand might be for a screen, power adapter and remote control, among other parts. The demand for the screen is dependent on the demand for the TV. Independent demand creates dependent demand.
What is an MPS?
A master production schedule enables companies to plan out their manufacturing needs. The MPS is based on independent demand.
Manufacturers use a master production schedule to understand the output they need to achieve to meet customer demand and to learn the amount of materials and parts they need to have on hand to meet scheduling and production line needs.
An MPS can benefit manufacturers by potentially decreasing inventory shortages or overages, reducing manufacturing costs, shortening lead times, reducing waste and boosting profit margins.
An MPS is one reference point for material requirements planning, along with existing inventory levels and a bill of materials.
What is MRP?
Manufacturers use software to conduct material requirements planning. MRP enables manufacturers to calculate and order the amount of components and parts they need to meet manufacturing needs.
Material requirements planning helps manufacturers create the following:
- Purchase orders for any needed additional parts, materials or components.
- Materials plans that lay out how the manufacturer uses the materials.
- Work orders, which ensure that labor and other resources are available when needed.
MRP can help reduce delays and improve forecasting and inventory management.
The differences between an MPS and MRP
MRP and an MPS focus on different aspects of manufacturing.
Material requirements planning helps manufacturers order the right materials so they have everything they need to produce dependent products.
By contrast, a manufacturer creates a master production schedule to determine when and how they use those materials to manufacture independent demand goods. An MPS can help ensure that the manufacturer meets customer requirements and minimizes the lead time to produce finished items.
Optimizing manufacturing processes relies on close integration between an MPS and MRP. This integration enables manufacturers to manage dependent and independent demand and maximize product availability.