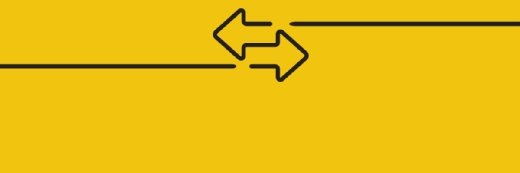
WMS vs. IMS: Learn the differences between the two systems
A WMS streamlines warehouse operations, while an IMS focuses solely on inventory management. Discover how these systems can work together to streamline warehouse processes.
Many organizations are likely using a warehouse management system, but they might benefit from adding an inventory management system as well. Supply chain leaders should learn about the differences between the two to determine if an inventory management system can help their company improve operations.
A warehouse management system (WMS) enables users to automate processes across many business areas, but the system's broad approach can lead to a WMS not fulfilling some companies' needs. One potential complementary product is an inventory management system (IMS).
Here's more about the differences between a WMS vs. an IMS.
What is a WMS?
Warehouse management includes many processes that can be difficult to track without an automated system. A WMS's automation capabilities can help improve inventory control, reduce manual work and track labor usage, among other benefits.
Companies often use a WMS alongside an ERP system, and the ERP can push data, such as product details, to the WMS. Because ERP software is meant to also serve other departments like HR and facilities, some companies might find their ERP's warehouse functionality lacking.
What is an IMS?
An IMS focuses on inventory management processes and helps users manage all the steps involved in inventory management, including purchasing, storing and tracking inventory.
Inventory management is a critical part of meeting sales objectives and managing costs. An IMS can provide insight into products' locations and how many are in stock. An IMS's data can also help supply chain leaders improve processes. For example, a company might reduce the price of inventory that the IMS identifies as slow-moving or return it to the original vendor.
An IMS can also help measure vendor performance, such as the amount of time it takes vendors to fulfill orders or the number of issues with delivered orders.
An IMS manages inventory processes at a much more granular level than a WMS or ERP system. Companies can use an IMS with a WMS or an ERP system. An interface between an IMS and a WMS can enable data sharing between the two systems, eliminating the need for entering data twice.
WMS vs. IMS
Companies might find it useful to add an IMS to their operations if their WMS is unable to accurately track inventory levels.
While a WMS can track inventory, companies with multiple warehouses or thousands of products might need more insight. An IMS can provide real-time inventory information, enabling supply chain leaders to adjust if needed. For example, if inventory at one warehouse is low, a user can move employees to fulfill orders at another warehouse until inventory at the original warehouse is replenished.
Both WMS and IMS offer reporting and dashboard features, but a WMS focuses on high-level inventory data, while an IMS's detailed inventory data enables more in-depth analysis.
While the IMS's information can help companies in various ways, some users might only require access to the WMS data, so setting up an interface between the two systems is important.
Eric St-Jean is an independent consultant with a particular focus on HR technology, project management and Microsoft Excel training and automation. He writes about numerous business and technology areas.