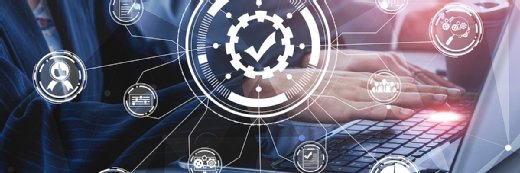
Getty Images
WMS vs. OMS: Learn the differences between the two systems
While WMS streamlines warehouse processes, OMS can help improve order management and customer data tracking. Discover more about the differences between WMS and OMS.
A warehouse management system can often help optimize internal processes. Leaders should consider adding an order management system to their operations for maximum efficiency.
While a WMS can automate and improve processes within a warehouse, the system often operates at a higher level than specialized systems. An OMS enables a company to further refine and automate processes related to customers' orders such as processing orders, fulfillment and inventory.
Learn more about the differences between a WMS vs. an OMS.
What is a WMS?
A WMS is a software application with broad functionality that helps manage processes across the warehouse. The system oversees steps in the supply chain process such as products arriving at the warehouse and customers receiving the items. It can automate manual processes, track orders and inventory and improve reporting and dashboards, among other benefits.
Companies often implement WMS software to complement their ERP systems. While some ERPs offer WMS functionality, it's often more high-level because of an ERP system's broad scope.
What is an OMS?
An OMS is a software application that specializes in order management, including tracking customer orders, fulfillment and billing. Organizations often use an OMS alongside a WMS and an ERP system. An OMS application is particularly helpful if a company uses many different sales channels, such as online stores, in-person stores and third-party sales, to sell products.
An OMS helps keep track of orders, ensures that inventory levels are sufficient to fulfill each order, and closes out the order once the customer receives the final product. The system also helps company leaders make better decisions by offering insights into the data captured through each process.
Some overlap in functionality exists between a WMS and an OMS. To address this overlap, some WMS vendors are expanding their software's functionalities to potentially eliminate the need for an additional OMS platform.
WMS vs. OMS
After an ERP implementation, adding a WMS is often the next logical step to improve warehouse operations.
However, as the company grows and increases its number of sales channels, the WMS's order management capabilities might no longer meet the company's needs. Implementing an OMS can help improve the order management process and improve employees' analysis of areas for improvement, among other aspects of operations.
An OMS might also be a necessary addition for companies with a WMS that otherwise fits their needs but has inadequate order management functionality. Fully replacing a WMS is a significant decision, so adding an OMS application can save the company time and money.
When a company uses a WMS and an OMS, data can travel between the OMS and WMS in real time, keeping both systems in sync. WMS users might not always require the detail that the OMS provides, but the OMS data might still be helpful to them. Similarly, OMS users might find it helpful to know when WMS data updates.
Eric St-Jean is an independent consultant with a particular focus on HR technology, project management and Microsoft Excel training and automation. He writes about numerous business and technology areas.