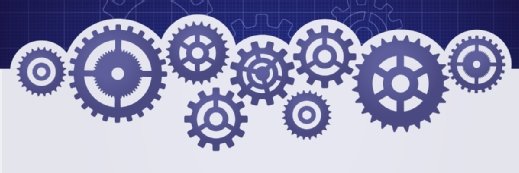
ERP vs. WMS: Which one is right for you?
If nuanced warehouse efficiency is necessary to fulfill customer expectations, an ERP system may not be enough. Here's what to consider when it comes to ERP vs. WMS.
For some companies, customer loyalty depends on a well-functioning warehouse -- and that may require specialized software.
Many companies rely on ERP software but may require a warehouse management system to meet the demand for specific functionalities.
Organizations with specific warehouse and inventory management needs may require a warehouse management system (WMS) in addition to ERP. Augmenting ERP with WMS might offer better support of an organization's goals and provide a competitive advantage.
Here's more about the differences between ERP and WMS, when adding a WMS might be necessary and the issues a new system won't solve.
What is ERP?
Companies use ERP systems to manage critical back-office functions on a single platform. One benefit of ERP is that many types of companies can use the software.
The broad scope of an ERP system means multiple departments can use, share and view data within dashboards and reports. For example, ERP can automate and simplify accounting, purchasing, human resource management and inventory management tasks.
ERP also reduces the need for numerous interfaces between systems and provides a consistent look and feel.
An ERP system may include basic warehouse and manufacturing functionality. For companies with complex needs, that functionality might not be enough.
What is a WMS?
A warehouse management system manages processes from the time products and inventory enter the warehouse until they leave. Companies with a warehouse or manufacturing facility may want to consider adding a WMS.
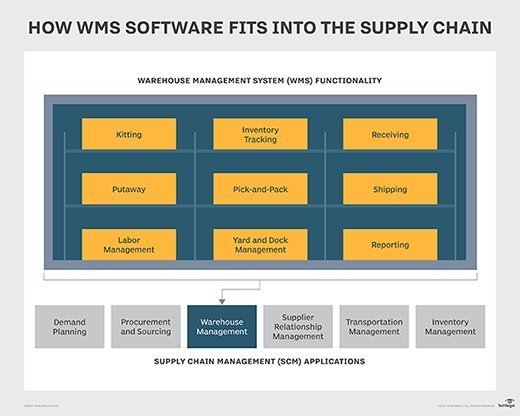
A WMS targets warehousing-specific needs, rather than offering functionality businesses can use across the entire organization. It provide the tools, dashboards and reports to ensure a warehouse operation is efficient and avoids downtime. This includes all the steps from acquiring materials to shipping the finished products from the warehouse.
A warehouse management system integrates with ERPs and other systems to provide functionality not offered in the WMS itself. For example, a company may want to use ERP for all finance-related transactions because it works across the company. A WMS would send any financial information it captures to the ERP for consolidation with other financial data.
Key differences between ERP and WMS software
Key differences between ERP and WMS software include the scope of functionality offered.
Essential aspects of ERP include the following:
- ERPs typically have a broad scope, offering features that can benefit the whole company.
- Companies from different markets can use ERP.
- ERP isn't restricted to a warehouse or manufacturing environment.
Key aspects of a WMS include the following:
- A WMS meets the needs of a warehouse or manufacturing facility.
- Because the scope of a WMS is narrower than what's offered through ERP, WMS vendors can spend their time and effort developing very detailed and feature-rich software for their specific market.
- The targeted functionality of a WMS often translates into additional configuration options that let a company set up the WMS to meet its needs, rather than how the vendor designed the system's usage.
When to invest in a WMS
There are multiple considerations to determine when the time is right to implement a WMS.
The sophistication of the company using the ERP software should be considered. Companies that have recently implemented an ERP system may find that system's warehouse functionality enough for their needs. Over time, however, it may become clear that only the additional features of a WMS will meet the company's warehouse management needs.
The size of the company also affects which types of systems should be implemented. Smaller companies might not have the resources to implement and maintain an ERP and WMS system. Having two systems requires an additional effort to input and maintain data so reports and dashboards provide valuable insights to management.
Buying teams might want to evaluate their current challenges to determine if they can justify the cost of another system. For example, how often the company has run out of supplies, lost track of inventory or been short-staffed will factor into buying criteria. If these and other issues happen on a regular basis, and the current systems aren't providing enough data to avoid these issues, buying teams should evaluate if and how a WMS system could resolve these problems.
When doing an analysis on the limitations of a company's current systems, it's important to determine if the problems are caused by missing functionality, data maintenance issues or some other issue.
If the problem is missing functionality, first consider if the current systems provide the necessary features. Often, companies fail to implement new features that vendors make available. If data cleanliness is the issue, it's important to understand why errors are happening. A new system won't solve data hygiene issues and might make them worse.
For example, employees might need training to ensure all the data they enter is accurate. Implementing a new system won't address the issue and might make the situation worse as employees now have to learn how to use a new system.
It's also possible the system isn't configured in a way that simplifies the collection and updating of data, such as when there are outdated items in picklists or unnecessary fields.