
supply chain planning (SCP)
What is supply chain planning (SCP)?
Supply chain planning (SCP) is the process of anticipating the demand for products and planning their materials and components, production, marketing, distribution and sale. Its overall goal is to balance supply and demand, so sales revenue opportunities are fully exploited in a timely manner and at the lowest possible cost.
Members of different internal teams -- such as sales, marketing and production -- work together to estimate product demand based on several factors, including historical data. Projections are then passed onto production and other teams that might need this information to maintain inventory. Organizations can also use SCP software suites that sit on top of a transactional system to provide features such as planning and what-if scenario analysis.
SCP is one of the two main categories of supply chain management, along with supply chain execution (SCE). The supply chain planning process was traditionally implemented by just large organizations, but today can be used by organizations of all sizes.
Supply chain planning steps
As a part of supply chain management, SCP works around planning and accounting for raw materials, suppliers, manufacturing, distribution and sales to customers.
This article is part of
Guide to supply chain management
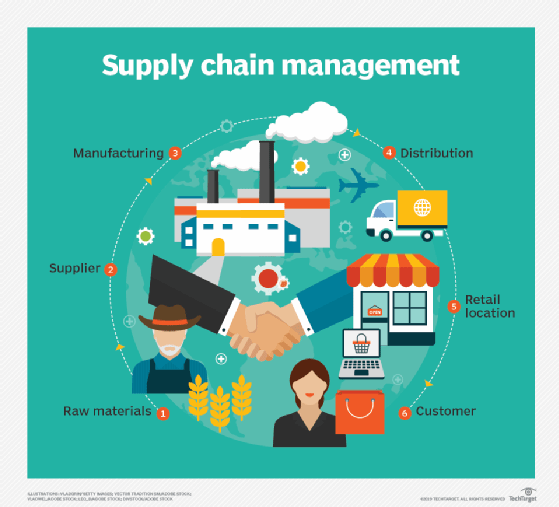
The supply chain planning process almost always begins with demand planning. Here a team of people from sales, marketing and production create a sales forecast based on historical data and other information, such as data arriving from point-of-sale (POS) terminals. The team then analyzes the data in spreadsheets, specialized demand planning software or data repositories to identify patterns that provide clues to future demand.
Demand planning often includes an attempt not just to forecast demand, but to influence it to some degree, through such mechanisms as price cuts, product substitutions and special promotions. This demand shaping is another tool that companies use to more closely match demand with the actual supply.
Once the demand plan is approved, it's translated into a corresponding production plan and, eventually, carried out in the various steps of supply chain execution, such as distribution and order fulfillment.
Key supply chain planning elements
At most companies, supply chain planning is accomplished using a collection of planning and forecasting processes and software. There's usually no single SCP software system, although many applications and supply chain management (SCM) suites are designed to facilitate end-to-end SCP by helping trading partners to collaborate.
Integration between different vendors' SCM systems and online procurement networks also facilitates SCP across geographic and corporate boundaries.
The main supply chain planning processes include the following:
Sales and operations planning (S&OP) is an effort to match a manufacturer's supply with customer needs and demand by having the sales department work with operations departments -- such as manufacturing, marketing and procurement -- to develop a single production plan. The S&OP team starts by gathering information, such as recent forecasts and sales and inventory data, develops a demand plan and builds a production plan based on available manufacturing and distribution capacity. The team then reconciles the demand and production plans against resource constraints -- such as finances -- before meeting with executives to adjust the plan and obtain their final approval. Some companies employ S&OP in a broader integrated business planning (IBP) process that rolls up the plans of other departments, such as finance and HR, into a single plan. In fact, IBP evolved from S&OP.
Material requirements planning (MRP) is a method for calculating and planning the raw materials and components needed to manufacture the products outlined in the demand or production plan. It involves taking inventory of materials and components, identifying others that are needed and making plans to produce or buy them. MRP's critical role in the supply chain is obvious, since it affects the supply coming into a manufacturer and leaving it in the form of products continuing along the chain to distributors, retailers and ultimately to consumers.
Manufacturers have used MRP since it was developed in the 1960s, and few manufacturers of any size do without it. Some also use a successor called manufacturing resource planning (MRP II) that includes MRP but broadens the concept to other operations of a manufacturer, such as shop-floor scheduling, purchasing and financial management. MRP II was broadened in the late 1980s to work in industries outside manufacturing, and Gartner came up with a new name – enterprise resource planning (ERP) – in 1990 to capture its appeal to any type of enterprise.
S&OP, IBP, MRP and MRP II all were processes before software vendors developed specialized modules for them. Today, most vendors of ERP suites – especially those expressly serving the manufacturing sector – have MRP modules and a handful have S&OP software, and fewer still sell IBP tools. There are dozens of niche MRP vendors.
Production planning addresses the details of manufacturing products, including the number and types of products, their components, who makes them and which plants and machinery are involved. Production scheduling is a key part of production planning and the term is sometimes used as a synonym for the entire process.
Advanced planning and scheduling (APS) goes beyond simple production planning in an attempt to optimize more of the factors that can affect supply, especially materials, labor and plant capacity. It can also incorporate demand management and, in theory, provides a much finer-tuned mechanism for matching supply with demand. Major ERP vendors, including Oracle and SAP, sell dedicated APS modules.
Importance of supply chain planning
Supply chain planning is a tactical approach that, when done well, helps optimize the manufacturing and delivery of products. It can lower production costs, increase sales and help manage relationships with suppliers.
With an effective supply chain strategy, an organization can properly anticipate demand and avoid having a surplus or a lack of inventory. Likewise, having a predefined backup plan helps mitigate potential supply chain disruptions.
SCP software also enables an organization to better communicate and work with suppliers. If an organization and its suppliers can see the same data, then the organization can make faster decisions or changes based around inventory.
Supply chain planning benefits
Effective supply chain planning implementation provides the following advantages:
- Improved data collection. Having access to precise, real-time data can improve decision-making and facilitate time-sensitive processes, such as just-in-time manufacturing.
- Enhanced inventory management. Up-to-date inventory data can enable lean production and lower overhead.
- Increased efficiency. Accurate demand and production plans can help an organization identify inefficiencies, including raw materials waste and excess inventory. This helps increase an organization's responsiveness.
- Improved customer satisfaction. Tracking customer sentiment and product demand can improve profit margins.
- Enhanced product lifecycle management. Demand planning can help align product development with consumer demand.
- Increased output. The improvement in communication that SCP provides also leads to better coordination and output among vendors, suppliers and organizations.
- Better cooperation. SCP facilitates cooperation among vendors, distributors and organizations, as increased communication is needed to anticipate demand for materials, components and inventory levels.
- Reduced delays. All parties involved in SCP should have a clear idea of their roles and responsibilities and ensure issues such as shortages or shipment delays are mitigated.
- Improved resource allocation. SCP enables more informed decisions to be made around resource allocation in a value chain.
- Reduced costs. SCP can reduce inventory, inventory management, shipment and operational costs.
Examples of supply chain planning
If a growing organization makes several acquisitions, then processes -- such as the allocation of resources or consolidating data across multiple systems -- could become a challenge. Using an SCP software suite, the organization can standardize new business processes while gaining visibility in supply and demand planning. SCP software tools typically include features such as data collection, demand forecasting, asset and business tracking, sales, operations and production planning, and process automation. These tools aid in the consolidation of systems and provide more visibility for resource allocation.
Likewise, if an organization's product suddenly increases in demand, then that organization can use SCP to aid in the planning, resource allocation, production and distribution of that product. SCP increases the visibility in the supply chain, allowing the organization to accurately plan production and distribution based around resource availability.
Learn more about the supply chain management process, including its importance, trends and challenges.