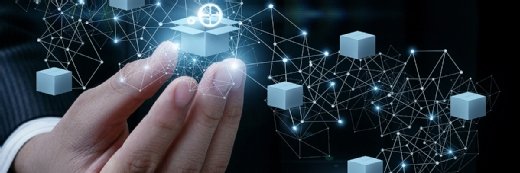
Getty Images/iStockphoto
7 3PL KPIs that can help you evaluate success
Supply chain leaders should look at some particular KPIs to determine whether their company's 3PL provider is meeting their needs. Learn the most helpful KPIs.
Third-party logistics providers provide a wide range of services to clients who want to outsource parts of the supply chain. Companies can use several KPIs to determine whether their current third-party logistics provider is meeting their needs.
Third-party logistics (3PL) provider KPIs measure how well a logistics company is performing when carrying out its services. Examples of 3PL KPIs can include the speed with which a 3PL fulfills orders and how well they maintain accurate inventory levels.
Here's a look at the difference between KPIs and some other performance measurements as well as some KPIs that supply chain leaders should make sure to include when examining their 3PL provider's performance.
The difference between KPIs, service level agreements and metrics
When examining 3PL KPIs, supply chain leaders should review the difference between metrics, KPIs and service level agreements, as the terms are closely linked but not the same.
The three terms are distinguished by the following characteristics:
- Metrics tend to be a lower-level measurement within an organization that indicates the operational performance of a department or team.
- KPIs are usually higher-level indicators that measure the progress of the company as a whole in achieving its, or a client's, goals. KPIs can represent the combination of multiple metrics.
- SLAs are contractually agreed-upon targets that a provider must meet. KPIs indicate how a provider is performing against those targets.
For example, a metric might be the speed with which the 3PL dispatch team picks and packs items, and the KPI would be the percentage of items dispatched within 24 hours. The SLA would state that the 3PL must dispatch at least 95% of items within 24 hours.
Here are seven of the most useful KPIs for supply chain leaders to consider when determining whether their 3PL is delivering services that are in line with their company's expectations.
1. Dock-to-stock time
One of the duties of a logistics service is receiving products into the warehouse and placing them in the correct storage areas, so the dock-to-stock KPI measures the length of time between taking the items into the warehouse dock and adding them to inventory storage. Warehouse workers cannot pick and dispatch products until they are put into stock and become available for order fulfillment.
A fast dock-to-stock time increases product availability and helps avoid the need for order cancellation because items are out of stock.
2. Cost per unit shipped
Cost per unit shipped indicates how much it costs the company to fulfill orders. Although supply chain leaders can measure and segment this KPI in various ways, it most commonly indicates the end-to-end cost to pick, pack and ship a product to its destination.
This KPI can take into account the price of storage, labor, packaging materials and other factors to indicate an all in cost. It's most useful to companies for tracking costs over time and managing order fulfillment expenses that negatively affect profit margins.
3. Inventory accuracy
Inventory accuracy is a comparison of physical stock levels in warehouse storage to the expected stock levels in the 3PL's warehouse management system software. WMS inventory levels can vary depending on the number of products received into the warehouse and order fulfillment, among other factors.
Processing products can lead to errors, so 3PL providers use physical counts of inventory to ensure that their WMS software accurately reflects actual stock levels. Any difference between WMS and physical stock will negatively affect inventory accuracy.
Companies and their 3PL provider can use the inventory accuracy KPI to identify inventory shrinkage. Some of the causes of inventory shrinkage are inaccurate picking and packing, problems when receiving goods and theft, among other factors. A 3PL can then look into the cause of the shrinkage.
4. Order accuracy
Order accuracy is the percentage of orders that workers picked and packed correctly. That process begins with the picker selecting the correct products based on the WMS's request. The picker then packs those items, secures the packaging and prepares the product for distribution.
Order accuracy is an important KPI because customers will likely lose trust in a company over time if they receive the wrong item. In addition, replacing an item costs the company more money because workers must repackage and replace the erroneous order.
5. Shipping accuracy
A shipping accuracy KPI is the percentage of products and packages that are delivered to the correct destination. Missing products can lead to significant frustration for customers, so shipping accuracy is critical for minimizing wastage, costs and customer dissatisfaction.
If shipping accuracy is too low, a 3PL provider will likely work with the distribution and transportation departments to reduce errors.
6. On-time shipping and delivery
The on-time shipping KPI typically indicates the length of time between the 3PL provider receiving the order and the time when the product is dispatched to its destination, while on-time delivery usually indicates the amount of time it takes for the customer to receive their product. Some 3PL providers combine these two factors into one KPI, while others measure them separately.
These KPIs are crucial for meeting customer expectations. Companies are under more pressure than ever to provide fast order fulfillment and delivery, so supply chain leaders must closely track their organization's shipping and delivery processes.
If a company offers priority shipping, supply chain leaders may also examine the success rate of that process to make sure their customers are receiving their orders as promised.
7. Reverse logistics and return processing
Part of selling products is dealing with the inevitable customer returns, and the process of returning goods to a 3PL is known as reverse logistics. 3PLs may measure a variety of KPIs for returns processing, including the time it takes to process returns and return rates due to order fulfillment or delivery errors.
Supply chain leaders can track returns processing times to check whether products are restocked quickly. Meanwhile, looking at return rates due to errors can help identify and resolve issues within the supply chain, leading to higher-quality order fulfillment.