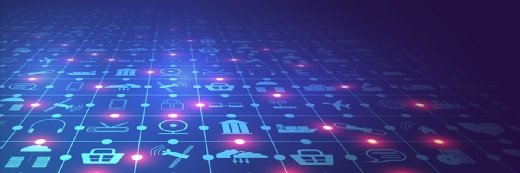
Getty Images/iStockphoto
5 best practices for enterprise asset management
Enterprise asset management can help companies prevent problems down the line, such as equipment failure. Learn some best practices to follow to bring about success.
Manufacturers' dependency on their production equipment means that any downtime due to equipment failure should be prevented if possible. Following some enterprise asset management best practices can help ensure operations are as unaffected by equipment issues as possible.
Many companies use an enterprise asset management (EAM) platform to help ensure that all their assets are operating optimally. In some cases, the software can make following EAM best practices easier.
Here are some best practices for enterprise asset management.
1. Ensure traceability of equipment
An essential part of enterprise asset management is knowing items' locations at all times.
Some maintenance departments track equipment in spreadsheets, but EAM software's ability to track every asset can help ensure that equipment like forklifts don't go missing or get put back in the wrong place by employees. Missing equipment can lead to production delays.
2. Stay alert about maintenance needs
A crucial part of enterprise asset management is taking action before a piece of equipment breaks or requires attention.
EAM software's automation capabilities can approve purchasing of parts when needed as well as notifying users when action such as routine maintenance is needed. Regularly carrying out maintenance instead of delaying it will help avoid any equipment breakdowns, and the automated notifications help avoid employees forgetting to do the maintenance.
3. Analyze data to improve enterprise asset management
Enterprise asset management always has room for improvement. Data can give insight into potential areas of operations that need fixing.
EAM software's reporting capabilities and analytics can give insight into repair trends and frequently requested parts, among other information. For example, EAM data may reveal that a piece of equipment has needed repairs three times over the last two months. Manufacturing leaders may decide to purchase a new piece of equipment instead of continuing to repair the old one.
4. Communicate about EAM strategies
Enterprise asset management requires frequent communication between employees. For example, a warehouse supervisor may see that a vehicle requires maintenance but forget to alert the maintenance team, delaying the fix.
EAM software helps the operations team communicate with the maintenance team. It can streamline approval processes and provide users with further details about purchase order requests as well as enabling them to add notes about certain assets. For example, the warehouse supervisor can add a note in the EAM software that a vehicle requires maintenance so the maintenance team can schedule it as quickly as possible.
5. Ensure that the right technology is in place
In addition to EAM software, enterprise asset management requires that end users possess the proper technology, such as tablets or mobile devices.
Manufacturing leaders should ensure that everyone who works with assets has the technology they need to quickly communicate about them. For example, if an employee who works on company vehicles doesn't have a mobile device, they have to wait until they can access EAM software to communicate about vehicle issues rather than notifying co-workers immediately.
Reda Chouffani runs a consulting practice he co-founded, Biz Technology Solutions Inc., and is CTO at New Charter Technologies. He is a technology consultant with a focus on healthcare and manufacturing, cloud expert and business intelligence architect who helps enterprises make the best use of technology.