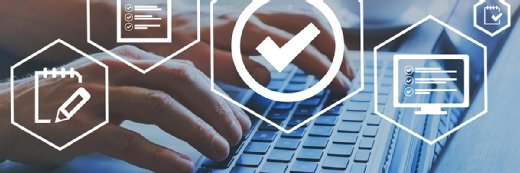
Getty Images/iStockphoto
PLM and PDM software: Learn the differences
PLM and PDM software may seem similar, but they fulfill different needs for manufacturers. Learn the differences and which is more useful for your company.
Companies use both product lifecycle management software and product data management software during the manufacturing process, but the two software types differ in important ways.
A PLM system helps employees manage a product from concept to retirement, potentially by integrating with other technology. Employees upload the data from each step in the process to the software. PDM software, on the other hand, helps employees manage the data associated with engineering activities.
Learn more about PLM and PDM software as well as the differences between the two.
What is PLM?
Manufacturers use product lifecycle management software to track and store data related to all aspects of a product. PLM systems are best for projects that produce a physical product rather than something less tangible, like software. The PLM software tracks new and updated files and data, ensuring that every employee can access needed information and is using the most up-to-date information.
A PLM system can integrate with other systems, such as ERP software.
What is PDM?
PDM software is a subset of PLM software. A PDM system helps employees track engineering data when developing or updating a product. Examples of data that users can add to a PDM include CAD files, 3D models, and design documents. A PDM can also automate processes, track change orders, and generate bills of material.
Using a PDM eliminates the need to share information through email and spreadsheets and ensures that everyone who needs it has access to the most current data. A PDM system can streamline work with third parties, such as external partners and consultants.
Should you choose PLM or PDM?
Both PLM and PDM software can help companies in various ways.
If a company is purchasing one or the other, the evaluation team should consider a few important factors. The team should first determine the budget allocated for the software, including implementation costs and annual licensing fees, as well as potential costs, such as consultant support, system integrations, and third-party software. PLM software usually costs more, so the team may need to eliminate it from the outset.
The team should next determine the problem that needs solving. PDM software can help address engineering-related problems with storing and tracking information, such as communication between engineering team members across time zones. A smaller company may find that PDM software fulfills its needs. But if the issues are broader in scope, a PLM system may be more appropriate. As a company grows, leaders may find PDM software no longer addresses their needs and the company requires a PLM system.
The urgency of the company's issues may also play a role in the decision to purchase PLM or PDM software. A company can implement a PDM system, which includes fewer features, much more quickly than a PLM. Also, implementing a PDM system likely requires a smaller team, so other employees can continue working on other projects.
Finally, the scope of the software may also be a factor in the decision-making process. More employees use a PLM system. Therefore, leaders of the departments that will use the PLM software -- like engineering, manufacturing and marketing -- will likely want to participate in the software selection and implementation process. On the other hand, since fewer employees use a PDM system, the implementation takes less time.