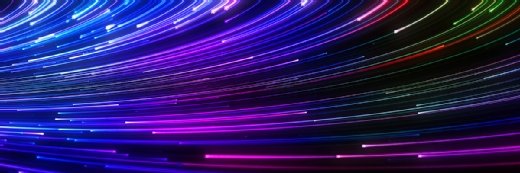
Getty Images
Keeping pace with different types of manufacturing processes
It's horses for courses in the industrial sector as partners look to help various kinds of manufacturers run on the emerging technologies that track with their needs.
Service providers pursuing digital transformation projects in the manufacturing vertical navigate a variety of niches with individualized needs.
The types of manufacturing processes include repetitive and discrete. Repetitive manufacturing revolves around high-volume production of the same part or product with little variance over long periods of time -- assembly lines aren't subject to change. In discrete manufacturing, products often change, and companies must frequently reconfigure production cells. Process manufacturing, meanwhile, uses a recipe or formula to create batches of products, from beverages to chemicals.
In addition, aerospace and defense manufacturing is considered a distinct industry sector due to the specialized and regulated nature of its products.
Those nuances add to the challenge of the manufacturing vertical, which features other complications such as diverse operations and locally autonomous factories. As a result, IT services providers must offer a different mix of technologies within the various manufacturing sectors or deploy the same types of technologies in different ways.
Tech for repetitive, discrete manufacturers
While all manufacturing sectors need emerging technologies to accelerate growth and productivity, each segment requires its own blend of technologies, said Paul Lewis, CTO at Pythian, an IT services company based in Ottawa. He pointed to the automation needs of repetitive and discrete manufacturers as one case in point.
"Repetitive production lines will focus much more on hyperautomation of production lines and integrated supply chains," Lewis said.
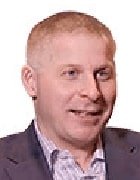
The hyperautomation field includes process mining tools for uncovering bottlenecks and robotic process automation (RPA) software for handling repetitive tasks. AI-based platforms such as computer vision also contribute to hyperautomation. Repetitive manufacturers can harness these technologies to boost the throughput of high-volume production lines.
Discrete production lines, in contrast, focus much more on speed of change automation, Lewis said. That is, they seek automation technologies that minimize downtime when a manufacturer modifies production lines to accommodate a significant change in product-assembly requirements.
Digital twin technology, which creates virtual versions of factory floor machinery, is another good fit for discrete manufacturers, Lewis said. Companies can create digital twins of machine combinations to test how they would work in a soon-to-be-modified production line. Lewis added that discrete manufacturers can also apply AI to craft new product plans, based on the availability of parts.
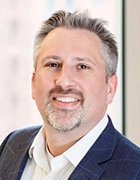
Discrete manufacturers also turn to IoT technology, but use cases aren't limited to the factory floor. Automotive and marine manufacturers, which sell through dealers, can embed IoT to create "connected experiences" that provide insight into how customers use their products, said Dan Neiweem, co-founder and principal at Avionos, a digital consultancy based in Chicago. Direct access to that information is a boon for companies that otherwise must rely on whatever data dealers are willing to share.
Once manufacturers understand user behavior, they can improve products and/or optimize their performance, Neiweem noted. They can also tap user data to promote other offerings in their product portfolios. "On the marketing side, customer usage data helps organizations find cross-sell and up-sell opportunities," he said.
In addition, manufacturers can invite customers to engage with their usage data through a mobile app or website. "This creates a conversation between the manufacturer and the customer," Neiweem said. A manufacturer can build brand loyalty on top of that IoT-connected experience, he added.
Process, discrete firms deploy AI differently
AI and machine learning (ML) play increasingly important roles in manufacturing, but the way industry sectors deploy the technologies varies. A process manufacturer, for example, follows the same formula so there's less variability among its production facilities. That makes it easier for a process company to scale AI and ML pilot deployments across the manufacturing enterprise, noted Bruce McKinnon, chief strategy architect at Insight, a solutions integrator with headquarters in Chandler, Ariz.
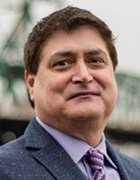
"Process manufacturers are a lot more scalable and can more easily leverage operational ML and AI models," he said, citing the example of one company that copied a single ML use case implementation across 18 plants. Process manufacturing is more scalable because there is little product customization and, typically, fewer process steps involved when transforming raw materials into a product, he explained.
Conditions in discrete manufacturing, however, impede the ability to scale AI and ML. With production lines subject to frequent change, a company would need to redo a model for each manufacturing cell, McKinnon said. But discrete companies can still reuse some AI and ML components, he added. They can standardize on methods for ingesting video in computer vision applications or approaches for operationalizing ML, for example.
Compliance needs in aerospace, defense
Aerospace and defense manufacturers, some of which have adopted emerging technologies such as 5G networking, present challenges endemic to that sector. The differences tend to cluster around security and compliance.
"Aerospace-defense may focus more on security or risk-related technology innovations, not necessarily for data loss protection, but for safety considerations," Pythian's Lewis said.
McKinnon said aerospace-defense, as well as other niches such as medical device manufacturing, have "more stringent compliance and regulatory concerns." Those issues may slow the pace of digital transformation, he noted.
For example, manufacturers suppling defense customers may not be permitted to change the product or the process through which it is made, McKinnon said. This "copy exact" requirement could rule out a digital transformation project, regardless of its potential for cutting costs and boosting efficiency, he noted.