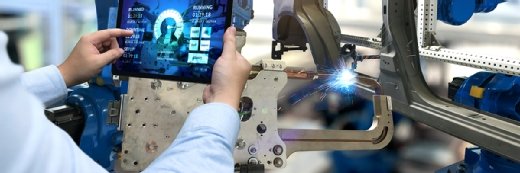
zapp2photo - stock.adobe.com
Words to go: Industry 4.0 basics
We've compiled a list of the key terms used to describe the fourth industrial revolution, as well as some of the technologies that are driving the vision forward.
One thing is certain: A fast-moving digital transformation is taking place in manufacturing as forward-thinking manufacturers bring advanced technologies, like AI, additive manufacturing and augmented reality, to factory floors. By connecting these technologies to systems and machinery across the supply chain, companies have begun to improve their production processes and customer satisfaction. What some people still may be uncertain of, however, is what to call this phenomenon -- this vision of a factory of the future.
This new era of manufacturing is often referred to as the fourth industrial revolution, or Industry 4.0. The name is a spinoff of Germany's government-based vision, coined Industrie 4.0, which calls for implementing and merging digital technologies in an industrial setting.
You've most likely heard the terms smart factory, smart manufacturing and industrial internet of things (IIoT), and while these terms are often used interchangeably, they are, in fact, different. But what do they mean exactly?
The following is a beginner's breakdown of the key terms used to describe the factory of the future phenomenon, or Industry 4.0, and the emerging technologies that are driving it.
Industry 4.0 key terms
Smart factory: Commonly referred to as the result of Industry 4.0, a smart factory is a manufacturing facility that runs on its own with the use of technologies like robots, AI and IoT. It is an environment that is strategically set up to improve the production process through three fundamental features -- visibility, connectivity and autonomy -- without the need of human intervention.
Smart manufacturing: Without smart manufacturing, there wouldn't be smart factories. It employs machines that are connected across multiple information systems and often outfitted with IoT sensors and other devices to track production processes and respond in real time. This way, manufacturers are better able to satisfy customer needs and keep up with ever-evolving demands in the factory and across the entire supply chain. Smart manufacturing gives companies the ability to analyze and address issues in real time, which, in turn, helps improve overall performance.
IIoT: The term IIoT has been used several times here to describe Industry 4.0, but what is it? IIoT is the use of IoT technologies to improve manufacturing processes. Blending technologies like machine learning, cloud-based data analytics and sensors, IIoT essentially creates systems that can collect and analyze data that helps manufacturers make better business decisions. It can also boost the return on capital investments through predictive maintenance and other asset management techniques.
Industry 4.0 technologies
Additive manufacturing: Additive manufacturing, also known as 3D printing, is the process of making parts from digital 3D models. Manufacturers use computer-aided design (CAD) programs to construct a digital model that is eventually sliced into layers. The 3D printer then lays down the layers from the bottom up to build the object. While additive manufacturing is still relatively new on factory floors, it is causing a stir with its potential as a cheaper, more efficient way to make just about any product, from standard car parts to parts for use in outer space.
AI: AI is a broad concept but can be defined as the simulation of human intelligence in computers and machines. In a factory, AI helps robots and other systems execute tasks and make decisions similar to a human. Machine learning, a subcategory of AI, goes one step further by not just mimicking human intelligence, but also being able to learn from experience. Manufacturers are implementing machine learning that can examine large quantities of real-time data and offer solutions, just like a human would.
Augmented reality (AR): AR is the integration of digital information into the user's environment and has become one of the most popular Industry 4.0 technologies. In a factory setting, workers can use AR technology while they are working to receive real-time information, such as images, documentation and data. For example, if a machine fails, the worker can use AR technology to look up information, compare digital images to the real-world object or speak with a remote specialist, which helps speed up troubleshooting and decision-making. A worker in a metal foundry might wear clear goggles outfitted with AR technology that show the temperature of the metal and other relevant information in the corner of the lens. AR can also be used as a training tool.
Collaborative robot (cobot): Autonomous robots that can perform one or two simple tasks have become common. But another type of robot -- the cobot -- is adept at taking on multiple tasks in order to assist factory workers. Cobots could lead to a coevolution of technology and humans rather than taking away factory jobs entirely.
Digital twin: A digital twin is a vital concept in IIoT. Similar to additive manufacturing, it is created in CAD or 3D design software and used to virtually represent a product. However, whereas additive manufacturing is typically used in the beginning stages of development, a digital twin is used throughout a product's lifespan. Sensors connected to the physical product can collect important data, send it back to the digital twin and ultimately help to enhance the product's performance.