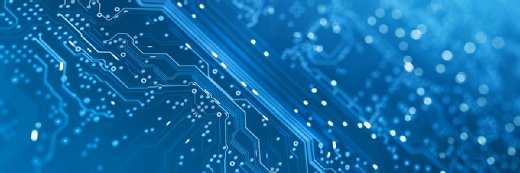
Getty Images/iStockphoto
10 core steps in the semiconductor manufacturing process
Semiconductors bridge conductors and insulators, enabling precise control of electrical flow. This complex process creates the foundation of modern electronics.
Semiconductors are a category of materials formulated to provide electrical conductivity somewhere between true conductors -- such as copper -- and true insulators -- such as porcelain.
The key to semiconductors is the ability to control their conductivity, allowing or blocking the flow of electricity. Control can be achieved by applying a stimulus to the semiconductor material. Typical stimulus includes temperature, voltage and light.
Common semiconductor base materials include silicon, germanium and gallium arsenide. Base materials are modified to adjust their desired conductivity characteristics by adding small impurities during the manufacturing process, called doping.
The potential to formulate desired conductivity and provide direct control over that conductivity makes semiconductors indispensable for all modern electronic components and devices. Examples of semiconductor devices include diodes, transistors and integrated circuits. These devices are used in computers, mobile devices, illumination, solar cells and sensors.
Semiconductor base materials occur naturally in the environment. However, they require a complex and sensitive process to manufacture practical materials with precise levels of doping to produce a practical semiconductor device at a production scale.
10 steps in the semiconductor manufacturing process
Typical semiconductor fabrication requires several key steps to convert raw materials into finished and packaged components ready for use in real-world devices. Some steps apply photographic techniques to establish and set elements. Other steps require chemical treatments and additional materials to develop elements and connections. And others yet apply heat to purify the components being manufactured. Each step in the manufacturing process involves significant inspection and testing -- often at the microscopic level -- to ensure the work-in-progress meets standards and performance requirements.
Semiconductors are manufactured in a fabrication plant or facility, usually just called a fab. Fabs are large and complex buildings built to house and operate many types of photographic, chemical and temperature application equipment tailored to the production of specific semiconductor products.
A common semiconductor manufacturing process includes the following:
- Design. The semiconductor manufacturing process begins with a comprehensive design of the device as it should be fabricated. This involves the development of detailed masks -- templates that will define the many microscopic components and interconnections that must be created on the semiconductor material wafer during manufacturing.
- Wafer preparation. Semiconductor wafers are cleaved as slices taken from a high-purity ingot of grown semiconductor material. Once a wafer is sliced into a thin circular wafer, it is cleaned, polished and inspected to ensure it is free of defects and suitable for fabrication. Finally, the wafer is chemically prepared, creating a thin oxide layer for the next process steps.
- Photolithography. A layer of chemical photoresist is applied to the wafer, a mask is placed over it and the wafer is exposed to light. Light exposure transfers the mask pattern to the wafer, which can then be developed to remove either the exposed or unexposed areas of photoresist -- not yet affecting the wafer material itself.
- Etching. At this point, chemical etching is used to remove wafer material from places where the photoresist has been removed. This starts the process of building and defining the features of the semiconductor structures within the wafer. Different etching processes and chemicals can be used depending on the specific wafer materials.
- Ion implantation and diffusion. Although semiconductor components are taking shape on the wafer, the components etched onto the wafer base material must be developed with specific electrical properties. Ion implantation uses dopants to chemically tailor the electrical properties of the wafer material. Once the wafer's electrical properties are correct, new chemical dopants are diffused into the wafer to enable specific electrical components, such as transistors.
- Annealing. The wafer is exposed to high temperatures in an annealing process designed to activate doping materials and effectively stop any further action of those chemicals -- basically fixing the fabricated components as they are.
- Deposition and oxidation. The components developed on the wafer must still be interconnected and insulated from one another. A deposition process -- such as chemical vapor deposition or physical vapor deposition -- is used to deposit thin films of metal conductor onto the wafer. This effectively ties all the components together properly. Oxidation grows a thin layer of silicon dioxide on the wafer to create insulation.
It's worth noting that these steps are often repeated several times, and the specific order of the steps can shift slightly, depending on the complexity of the semiconductor products being manufactured onto the wafer. Testing and inspection are frequent throughout the fabrication. Defects that commonly arise during fabrication reduce the number of useful components that can be derived from the finished wafer.
The completed wafer can then move on to the final stages of assembly and packaging, which include the following:
- Dicing. In a fabrication run, hundreds of semiconductor components -- such as integrated circuits -- can be developed on a single wafer. These finished components are cut, turning the wafer into individual chips.
- Assembly. Each chip is mounted on a foundation, wired to pins -- places where the semiconductor chip connects to physical contacts that interconnect with outside circuits -- and placed into protective packages.
- Final testing and packaging. The completed chip undergoes a final test to verify it is fully functional and meets required performance specifications. If the device passes final testing, it can be packaged for sale.
Challenges faced in semiconductor manufacturing
Semiconductor manufacturing is one of the most capital- and material-intensive industries in operation today, making semiconductor manufacturing a risky vertical. A common summary of the challenges faced in semiconductor manufacturing includes the following:
- Materials. Purity is critical due to the microscopic structures being built. Any impurity will likely ruin the product. Some semiconductor base materials are quite rare. Most materials demand a purity level that is difficult to achieve. This combination of scarcity and purity carry significant material costs.
- Toxicity. Many materials and chemicals involved in semiconductor manufacturing are highly toxic and generally expensive. Examples include heavy metals, corrosive acids, dangerous gases, volatile solvents and an array of toxic byproducts of the manufacturing process. These toxins require extreme care in storage, handling and disposal -- underscored by onerous regulations and worker safety concerns.
- Fab overhead. Semiconductor fabrication facilities are expensive and time-consuming to design, build, commission and operate. Fabs are also not universal -- one fab cannot produce any semiconductor device. Each fab is built to manufacture a certain limited range of devices. Although a fab can potentially be renovated, upgraded or repurposed, a fab has a practical lifecycle.
- Technology. Today's most complex semiconductor devices require photolithographic equipment and processes operating at the microscopic scale -- often in terms of just a few nanometers. The manufacturing equipment is custom-built, requires careful maintenance and high levels of worker skill. Each new generation of semiconductor device leverages a new generation of fabrication technology.
- Limitations. Semiconductor fabrication has essentially reached the limits of Moore's Law -- it is almost impossible to create equipment and processes capable of building significantly smaller semiconductors without new advances in photolithography and related processes. This demands extraordinary investments for only incremental fabrication improvements and has led to alternative advances in technologies -- such as parallel computing and quantum computing.
Future trends in semiconductor manufacturing
Despite challenges, semiconductor manufacturing has the potential to benefit from several future trends, including the following:
- ML, AI and IoT. Machine learning and AI technologies are being adapted to semiconductor manufacturing. This allows manufacturers to use a vast amount of fabrication process, equipment, quality and yield data to create important models for predictive maintenance, improved yield and process optimizations. Moreover, IoT devices are gaining acceptance across semiconductor fabs as a means to collect real-time information, often bringing that information into ML and AI platforms.
- New device formations. Techniques such as 3D chip stacking don't really create smaller devices, but instead create larger and more efficient collections of associated devices to offer features such as better power efficiency, better performance and higher operational bandwidth.
- Advanced lithography. Despite challenges, photolithography processes continue to advance slowly, and techniques such as advanced node manufacturing will continue to increase transistor density and performance of semiconductor devices.
- New materials. Semiconductor manufacturers are discovering and implementing new materials such as graphene, gallium nitride and boron arsenide. These materials offer the potential to enhance device capabilities such as power demands, performance, size and cost.
Stephen J. Bigelow, senior technology editor at TechTarget, has more than 30 years of technical writing experience in the PC and technology industry.