programmable logic controller (PLC)
What is a programmable logic controller (PLC)?
A programmable logic controller (PLC) is a small, modular, solid-state computer with customized instructions for performing a particular task. PLCs, used in various industrial control systems (ICSes), have primarily replaced mechanical relays, drum sequencers and cam timers.
PLCs have revolutionized the way industrial processes are controlled. They have enabled the automation of complex tasks, improved efficiency and reduced costs.
What does a programmable logic controller do?
PLCs are useful tools for repeatable processes because they have no mechanical parts and can gather information. Each central processor unit (CPU) continually loops through an input scan, program scan, output scan and housekeeping mode, repetitively performing a single task while monitoring conditions. The information the controller gathers can be used as feedback to guide needed changes and process improvements, some of which can be performed automatically according to the device's coding.
PLCs are common across many industries and are designed to be rugged and thrive in harsh environments with extreme temperatures, humidity and vibrations.
Some industries that use PLCs in their operations include:
- Building automation.
- Water treatment.
- Oil and gas.
- Manufacturing.
- Power generation.
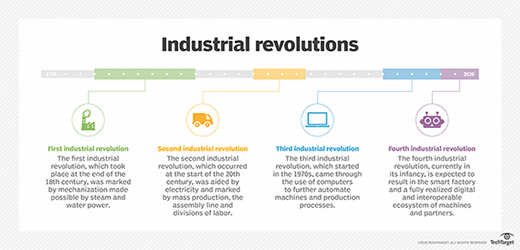
What are programmable logic controllers used for?
The primary purpose of PLCs is to automate industrial processes such as robotic devices, assembly lines and machines. PLCs are popular as they take up less space, perform more complex tasks and are more customizable than the mechanical technologies they have replaced.
PLCs are known for their ability to operate continuously without maintenance and have significantly impacted the digitization of many industries, particularly manufacturing. The first PLC, for example, was invented by Dick Morley in 1969 for General Motors and performed uninterrupted for 20 years before it was retired.
How does a programmable logic controller work?
The CPU is essentially the brain of the PLC and interprets program instructions and executes them. Input/output (I/O) modules deliver signals from sensors and switches (i.e., inputs) to the PLC and send signals to control devices like motors, valves and lights (i.e., outputs). The power supply unit converts AC voltage to DC voltage to power the PLC. Finally, the computer or another device used to create and upload the PLC program allows users to create instructions that tell the PLC what to do in response to different inputs.
As specified by the International Electrotechnical Commission (IEC) 61131, five programming languages are used to code PLCs:
- Ladder Logic.
- Function Block Diagram.
- Structured Text.
- Instruction List.
- Sequential Function Chart.
The controller can be recoded in place if significant code changes are required and the PLC's memory is embedded. When the PLC's memory is not embedded in the circuit board and substantial code changes are needed, the memory can be removed from an exterior slot on the PLC and replaced without requiring the assistance of a programmer on site.
For example, the sensors and switches will transmit signals to the PLC's input modules. Upon receipt, the PLC's CPU will read the signals from the input modules and automatically execute the predefined program instructions. The CPU will transmit signals to the output modules based on the program instructions. The output modules will then activate the control devices (motors, valves and lights).
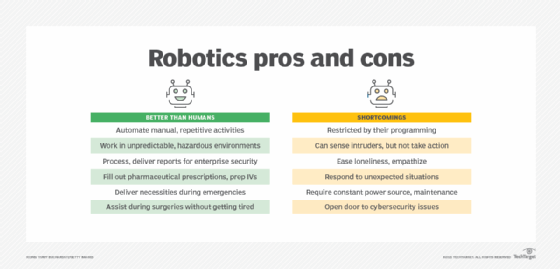
What is a safety programmable logic controller?
A safety programmable logic controller (safety PLC) is a type of PLC that is customized for critical safety applications in industrial environments. A safety PLC has all the standard PLC features but also has additional features and functionalities focused on ensuring the safety of personnel, equipment and the environment.
Both standard PLCs and safety PLCs can automate industrial processes, leverage similar programming concepts and have both CPUs and I/O modules. However, safety PLCs are designed to meet strict regulations and safety standards, minimize the risk of failure using redundant hardware, continuously monitor and test their own health and performance, boast safety-rated I/O modules, have limited flexibility, and follow strict programming and validation processes.
Where can you find programmable logic controllers?
PLCs are everywhere. The following are some everyday examples of where you might encounter PLCs:
- Amusement park rides.
- Automated car washes.
- Automated packaging lines.
- Building management systems.
- Traffic lights.
You can also find PLCs in automobile assembly lines, robotic surgery, semiconductor fabrication, food and beverage packaging, and networking and communications protocols.
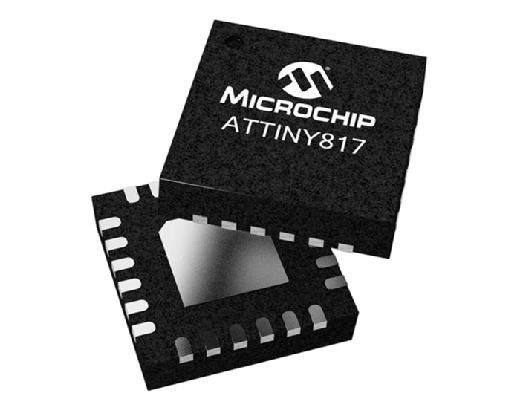
What are the benefits of using programmable logic controllers?
PLCs offer many benefits, especially when compared to those of traditional control systems like relay logic. Some of these key advantages include:
- Increased flexibility. PLCs can be programmed quickly. This makes modifying and adapting their behavior to rapidly changing needs or process requirements easy. PLCs help eliminate the need for complex rewiring demanded by standard relay-based systems. As such, PLCs are ideal for dynamic environments.
- Improved reliability. PLCs are rugged devices. Built for industrial environments, they can withstand harsh conditions, including extreme temperatures. Most PLCs today have built-in diagnostics and error-handling capabilities. This makes them much more reliable than their relay counterparts.
- Highly scalable. Users can quickly scale PLCs up or down to meet the changing needs of the application. For example, they can add or remove I/O modules as needed. Users can also leverage a single platform to control a machine or an entire production line.
- Real-time operation. As PLCs operate in real time, they can quickly and efficiently respond to changes in inputs and sensor data. This can be vital to applications demanding precise timing and rapid reactions.
- Efficient data management. PLC users can monitor and analyze process performance, identify trends and make informed decisions by collecting and storing data from various sensors and devices.
- Reduced costs. Although the initial investment in a PLC is often significant, its ability to improve efficiency, reduce downtime and minimize maintenance costs can lead to substantial cost savings in the long term.
- Enhanced safety. PLCs programmed with safety features and interlocks can help prevent accidents and injuries in hazardous environments. Organizations can benefit from added protection by integrating PLCs with safety devices like emergency shutdown systems.
- Seamless maintenance. PLCs simplify troubleshooting and maintenance processes. The modular design of PLCs enables simple troubleshooting and maintenance. For example, it's easy to replace faulty components, and diagnostic features can quickly pinpoint exactly where problems are, minimizing downtime.
- User-friendly programming. Modern PLCs boast user-friendly programming languages and software, so they're much easier to learn and operate than complex relay logic systems. This allows organizations to engage a broader range of personnel to be involved in system development and maintenance.
- Longer lifespan. Built to last in harsh environments, PLCs are known for their durability and long lifespan.
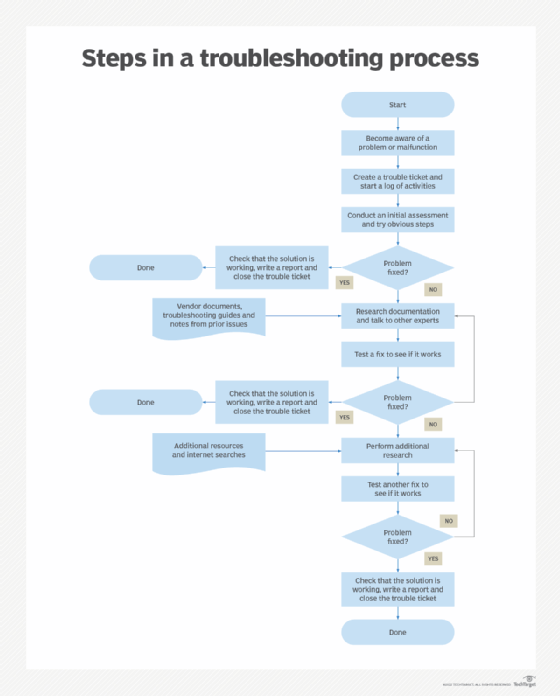
Overall, PLCs trump traditional control systems in many areas, making them popular for various industrial automation applications.